A wide variety of products in diverse fields of application can take advantage of free radical emulsion polymerization. They go from paints, coatings and adhesives to cosmetics, sealants, drug delivery systems, textiles and automotive products.1 This versatile technique allows the production of aqueous dispersions of polymer particles stabilized by a colloid stabilizer that present innumerous advantages.
Even though the technique is relatively recent, natural latex has already been exploited by different cultures for centuries. Natural rubber is an aqueous dispersion of polyisoprene particles stabilized by proteinaceous surfactants produced at room temperature by the rubber tree Hevea brasiliensis. It was from the observation of natural rubber by industrial chemists, and their wish to duplicate these conditions, that emulsion polymerization was born. During World War II, shortages in supply of this crucial natural material resulted in an acceleration of the production of synthetic latexes by emulsion polymerization.
While the early history of emulsion polymerization is strongly connected to the production of synthetic rubber, the modern era of the technique is more diversified. Indeed, the development of organometallic catalysts (that allow better control of polymer architecture) detached the manufacture of synthetic rubber from emulsion polymerization. But, after World War II, the extension of the technique to a wide variety of plastics opened a whole new range of applications to synthetic polymer latexes.
Similar to other dispersed-phase polymerization techniques, such as suspension, dispersion or miniemulsion, emulsion polymerization is performed in heterogeneous media and have water as the most common continuous phase. With growing environmental legislations to control the emission of volatile organic compounds, the possibility to produce waterborne latexes is an appealing environmental advantage, as water is inexpensive and nontoxic. The replacement of solvent-based paints by water-based paints, for example, has been possible thanks to emulsion polymerization. Since the solvent used in paints has a great impact on people’s health and on the environment, this has been a major advancement on paints technology.
Besides environmental and health aspects, another key feature of dispersed-phase polymerization is the relatively low viscosity of the system, even for high solids contents, compared to polymer solutions, which translates into low operational cost requirements. As viscosity is controlled by the viscosity of the continuous phase (water), it remains low even at high monomer conversions. In addition, since water provides a medium for heat transfer, temperature control is favored during the polymerization process. Therefore, agitation is facilitated, and simple heat removal technologies are necessary. Indeed, overheating can be a critical issue in the case of exothermic reactions such as most industrial polyolefin resins, for example. If the heat of reaction is not properly removed by the surrounding fluid, there might be significant and even dangerous temperature rises in the reactor.2
Some other important features of emulsion polymerization include the ability to produce polymer chains with high molar mass at relatively high reaction rates in comparison to other methods of free-radical polymerization such as bulk, solution or suspension, the ability to control submicron particle size and morphology, tolerance to a wide range of monomers, possibility to produce polymers that are extremely sticky and easy processability – product can be easily removed from reactor (and washed out with water) and latex can be used directly, in the case of coatings applications, or polymers can be easily separated from the latex.
While these unique features make emulsion polymerization so special and appreciated, the mechanisms that allow the polymerization of monomers relatively insoluble in a solvent to produce a polymer latex are also expected to be unique. To understand the mechanism of emulsion polymerization, it is important to acknowledge that besides water, monomer and a water-soluble initiator, another crucial ingredient should be present: the surfactant. When in water, surfactant molecules tend to assemble into micelles above a certain concentration (known as Critical Micelle Concentration, CMC) in order to minimize their surface energy. In such micelles, the hydrophilic heads of the surfactant are located outside, protecting the hydrophobic core from water. Monomer molecules can be either adsorbed by the micelles, dispersed as droplets that are stabilized by adsorbed surfactant molecules (majority), or soluble in the water phase, in a small fraction, which is crucial for the initiation process.
During initiation, the water-soluble free radical initiator suffers decomposition in the aqueous phase, generating radicals that react with the water-soluble portion of monomer. These propagating radicals grow in the water phase by the addition of a few monomer units, generating oligoradicals, until their length compromises their solubility in water. At this point, they become sufficiently hydrophobic to either migrate to inside the micelles (in a micellar nucleation process), or precipitate (homogeneous or coagulative nucleation). The micelles become, then, the main polymerization loci, allowing polymerization to proceed inside these new small particles. This first phase of polymerization, known as Interval I, is a transitory and quick phase, in which particle nucleation takes place and polymerization rate increases until the number of particles is defined (conversion generally goes from 0 to 15%). Then the second phase starts (Interval II). The particles that were nucleated in the previous step grow by the consumption of the monomer present in the swollen particles. These particles are constantly fed with the monomer present in the monomer droplets that diffuses through the water phase. During this interval, the number of particles and the polymerization rate stay constant. Particles grow in size, while the monomer droplets decrease until their total disappearance. After the total consumption of monomer droplets (at conversions of 80 to 90%, depending on the solubility of the monomer in the aqueous phase), the transition between phases II and III occurs. During interval III, polymerization rate decreases progressively, since only the monomer from the particles is present in the system, and it is gradually disappearing. The final product of emulsion, the latex, is an aqueous dispersion of solid polymer particles (with diameters of around 50 to 500 nm) that are stabilized by the surfactant molecules. The three regimes, or intervals, that can be identified in emulsion polymerization are illustrated in Figure 1.3
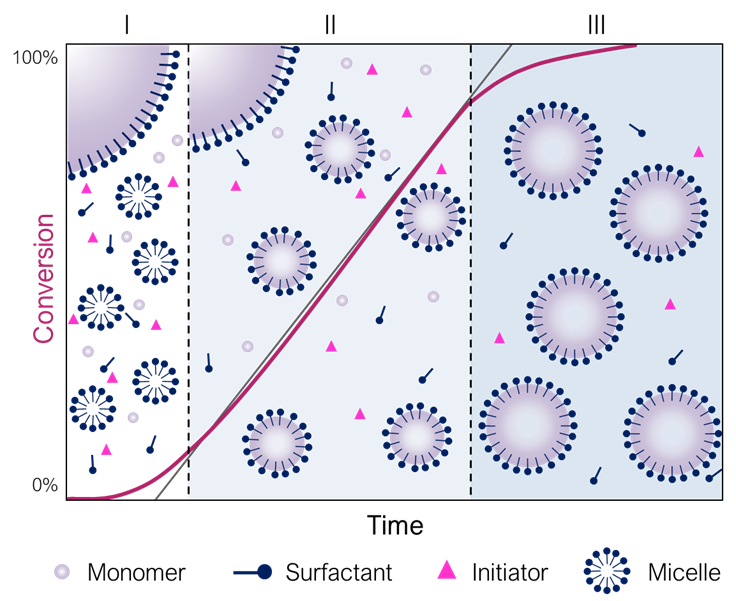
The presence of surfactants, however, can be responsible for some limitations of emulsion polymerization. When latexes are used directly, in the case of coatings applications, such molecules tend to migrate to the film–air interface, altering the final performances and properties of the coating (especially the interfacial properties such as wettability and adhesion, or permeability). When coagulation of the polymer and removal of the aqueous phase is necessary, polymers can easily become contaminated with traces of the emulsifier, which can lead to poor transparency.
To overcome these limitations, the benefits of emulsion polymerization have been associated to the advantages of controlled radical polymerization (CRP) in the development of surfactant-free emulsion polymerization. In the so-called polymerization-induced self-assembly (PISA) process, amphiphilic block copolymers are formed in situ via CRP.4 These amphiphilic molecules are able to self-assemble and act as steric or electrosteric surfactants, generating self-stabilizing latex particles while controlling the particle growth, in the absence of any additional conventional surfactant.
Even though emulsion polymerization is considered to be a more sustainable technique thanks to the use of water as continuous phase, it is worth mentioning that the rest of the recipe (~50%–55%) can still consist of predominantly petroleum-based raw materials. To further increase the sustainability aspect of emulsion polymerization, accordingly to the “12 principles of green chemistry and engineering”, it is essential to favor renewable biobased feedstock.5 In recent years, an increasing amount of effort has been dedicated to finding more sustainable and less hazardous monomers,6 emulsifiers, crosslinkers, chain transfer agents and fillers for emulsion polymerization systems. While biobased surfactants and detergent is a booming market thanks to increased demand by consumers and users,7 the sector of biobased monomers is more timid. Mainly coming from biomass feedstock, these novel materials generally contain various functions (alcohols, phenols, carboxylic acids, amines, among others) that allow their direct copolymerization by step growth polymerization in bulk or solution. The use of biomass for chain growth polymerization, however, is still more challenging, since they contain fewer suitable reactive functions for radical polymerization. Nevertheless, an increasing number of works dedicated to finding radically polymerizable biobased monomers, such as acrylic acid, methacrylic acid, myrcene or itaconate-based monomers can be found.6
References (1) Hungenberg, K.-D.; Jahns, E. Trends in Emulsion Polymerization Processes from an Industrial Perspective. In Polymer Reaction Engineering of Dispersed Systems: Volume I; Pauer, W., Ed.; Advances in Polymer Science; Springer International Publishing: Cham, 2018; pp 195–214. https://doi.org/10.1007/12_2017_14. (2) Floyd, S.; Choi, K. Y.; Taylor, T. W.; Ray, W. H. Polymerization of Olefins through Heterogeneous Catalysis. III. Polymer Particle Modelling with an Analysis of Intraparticle Heat and Mass Transfer Effects. J. Appl. Polym. Sci. 1986, 32 (1), 2935–2960. https://doi.org/10.1002/app.1986.070320108. (3) Smith, W. V.; Ewart, R. H. Kinetics of Emulsion Polymerization. J. Chem. Phys. 1948, 16 (6), 592–599. https://doi.org/10.1063/1.1746951. (4) Charleux, B.; Delaittre, G.; Rieger, J.; D’Agosto, F. Polymerization-Induced Self-Assembly: From Soluble Macromolecules to Block Copolymer Nano-Objects in One Step. Macromolecules 2012, 45 (17), 6753–6765. https://doi.org/10.1021/ma300713f. (5) Zhang, Y.; Dubé, M. A. Green Emulsion Polymerization Technology. In Polymer Reaction Engineering of Dispersed Systems: Volume I; Pauer, W., Ed.; Springer International Publishing: Cham, 2018; pp 65–100. https://doi.org/10.1007/12_2017_8. (6) Molina-Gutiérrez, S.; Ladmiral, V.; Bongiovanni, R.; Caillol, S.; Lacroix-Desmazes, P. Radical Polymerization of Biobased Monomers in Aqueous Dispersed Media. Green Chem. 2019, 21 (1), 36–53. https://doi.org/10.1039/C8GC02277A. (7) Hayes, D. G.; Smith, G. A. Chapter 1 - Biobased Surfactants: Overview and Industrial State of the Art. In Biobased Surfactants (Second Edition); Hayes, D. G., Solaiman, D. K. Y., Ashby, R. D., Eds.; AOCS Press, 2019; pp 3–38. https://doi.org/10.1016/B978-0-12-812705-6.00001-0. (8) Lovell, P. A.; Schork, F. J. Fundamentals of Emulsion Polymerization. Biomacromolecules 2020, 21 (11), 4396–4441. https://doi.org/10.1021/acs.biomac.0c00769.