Polyurethanes (PUs) were discovered in the 1930s by Otto Bayer and were mainly used to replace natural rubbers during World War II 4. Their global production accounts for 25.1 million tons in 2019.1 PU represent the 6th largest class of polymers 2 behind polyethylene (PE), polypropylene (PP), polyvinyl chloride (PVC), and polyethylene terephthalate (PET).3 PU are mainly used in three main areas: flexible foams, rigid foams, and nonporous materials (Figure 1). 2 Flexible foams are mainly used for comfort applications, such as mattresses or sofas, rigid foams are used for insulation, especially in the building industry, and the last area includes all products used in coatings, adhesives, paints and elastomers for example.
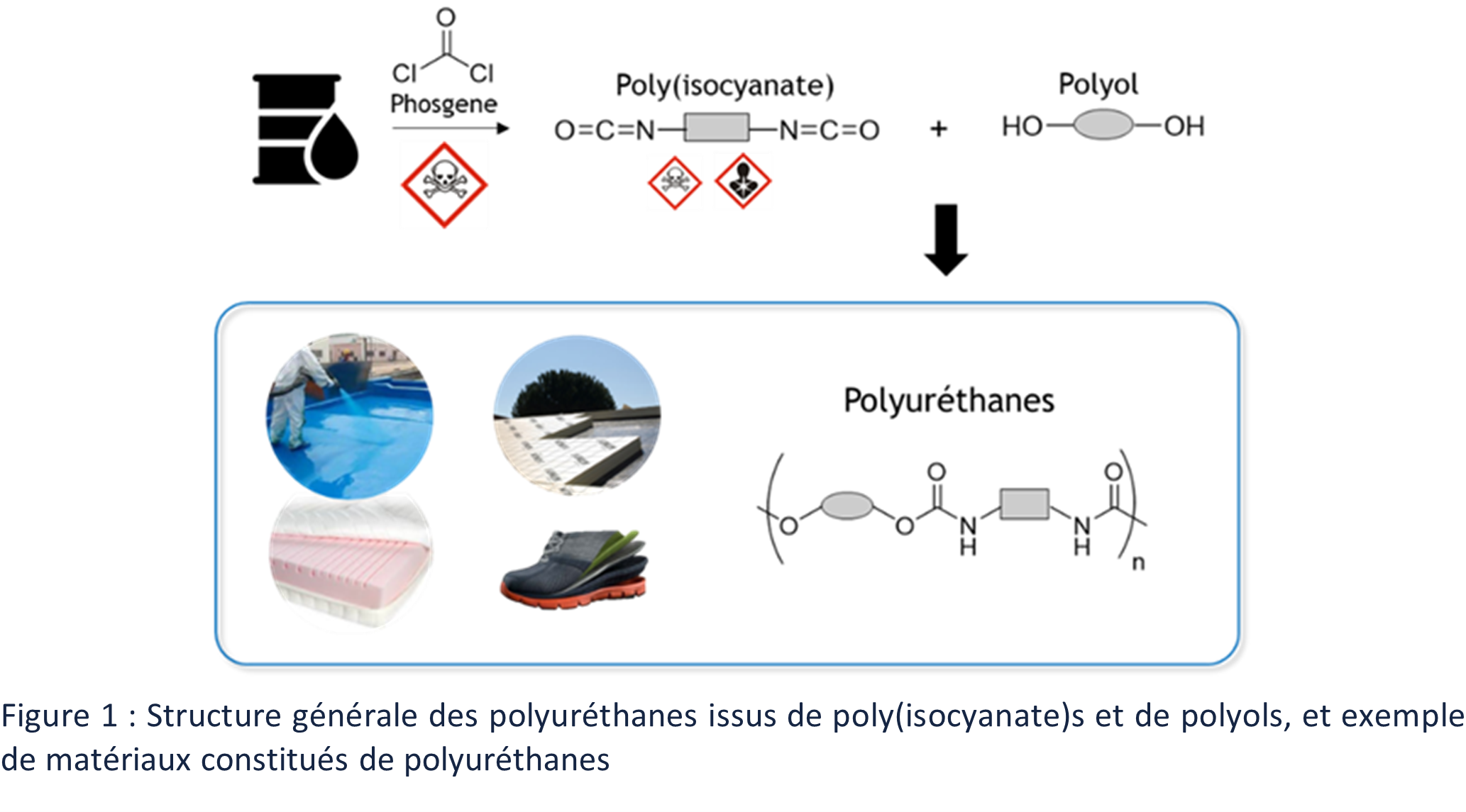
Classically, polyurethanes are synthesized by polyaddition of diols (or polyols) and diisocyanates (or polyisocyanates) (Figure 1).4 The availability of polyols and polyisocyanates allows the generation of a very wide range of materials with diverse properties.4
Despite the many advantages of PUs, their synthesis can be problematic. Indeed, the phosgene at the origin of isocyanates is a deadly gas and isocyanates are classified as CMR (Carcinogenic, Mutagenic and Reprotoxic), thus very toxic for humans.2 Moreover, as for the vast majority of polymers, PUs are mainly derived from fossil resources. The synthesis of biosourced isocyanates is possible, but their hazardousness remains problematic.5 In order to limit the risks for producers and users, alternatives to the synthesis of PUs, by “isocyanate-free” process, have been studied and developed. They lead to the formation of polymers commonly known as non-isocyanate polyurethanes (NIPUs).
The synthesis routes and properties of NIPUs have been studied for many years. Several scientific reviews have been published summarizing these different synthetic routes.2,4,6–11 They can be grouped into four types of polymerizations: by polycondensation, by polyaddition, by rearrangement reactions and by ring opening (Figure 2). Many efforts have been made to develop greener and less hazardous synthetic routes for PUs. Unfortunately, while many of these have eliminated the use of isocyanates, they have not eliminated the use of hazardous compounds. The use of phosgene, chlorides or azides is still necessary for the synthesis of PU precursors or for their synthesis.
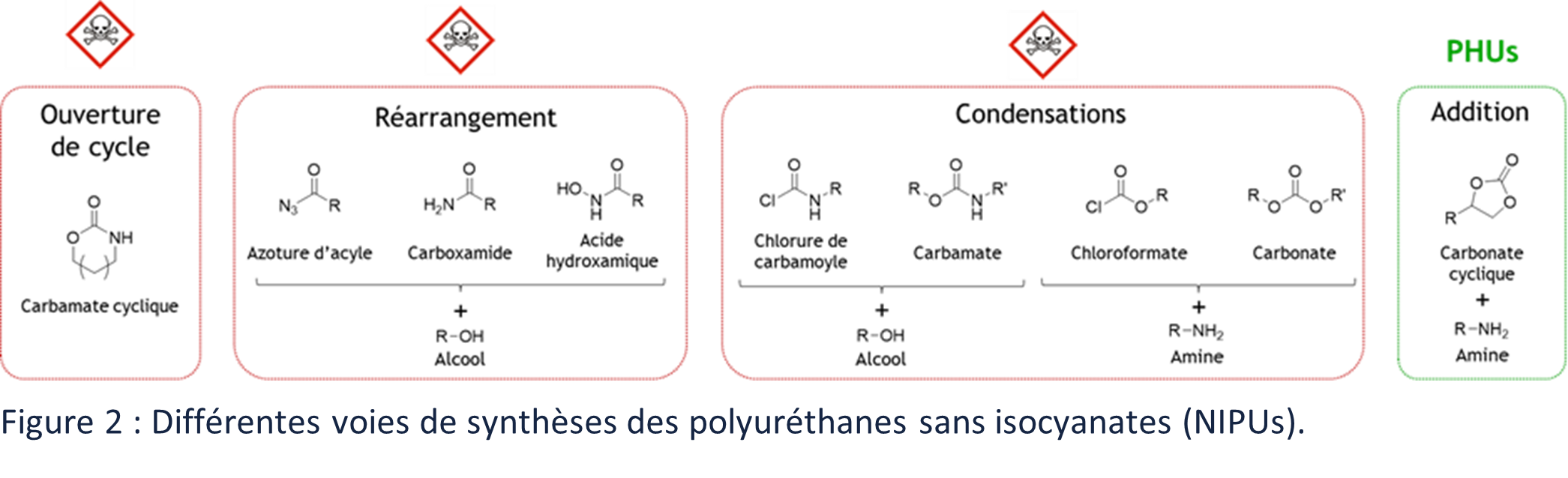
In addition to limiting chemical risks, the interest in finding alternatives to PUs is also to produce materials of renewable origin. Promising synthetic routes, which have been studied extensively in recent years, involve the polycondensation of bis-carbamates and polyols or the polyaddition of cyclic polycarbonates (CCs) and pluri-amines (Figure 2).2,6 The latter synthetic route leads to poly(hydroxy-urethane)s (PHUs), which can be, to a large extent, bio-based. These polymers have the capacity to respond to the problems mentioned.
Carbonates are rarely available naturally. A review by Zhang et al 12 refers to a few, however. These are mainly monocarbonates from plants (terpenoid carbonates), generated by bacteria or produced by fungi. Biobased cyclic polycarbonates are no more available naturally or synthetically, with a few exceptions. Recently, Wang et al 13 sought to reference biobased molecules that could lead to cyclic carbonates for PHU synthesis. The computer program developed by the research team was able to target nearly 40,000 potential CCs molecules, after one or two synthesis steps, from 15 biobased molecules. Numerous routes for the synthesis of cyclic carbonates have also been developed and very well described by different research teams, the main ones being described below.
A first family of cyclic polycarbonates can be synthesized from carboxylic acids or their derivatives and glycerol carbonate (GC) (Figure 3). These are the so-called “ester-activated” cyclic dicarbonates.

Specifically, cyclic ester-activated polycarbonates are obtained by derivatization of acids by reaction with glycerol carbonate.14–17 The acids can also be substituted by their derivatives, acyl chlorides, to react with glycerol carbonate.18–26 Currently, the synthesis of ester-activated CCs has several limitations in order to produce fully biobased polymers. On the one hand, glycerol carbonate is not fully biobased and on the other hand, the derivatization process of acid derivatives needs to be optimized in order to limit the use of toxic solvents or reagents and thus better comply with green chemistry principles.27
The second widely described route for the synthesis of biobased CCs is the carbonation of epoxides using CO2 (Figure 4).6,17,28–55 This synthetic route allows the valorization of carbon dioxide, which is generally fixed on epoxides by a catalyzed process at high temperature and high pressure.
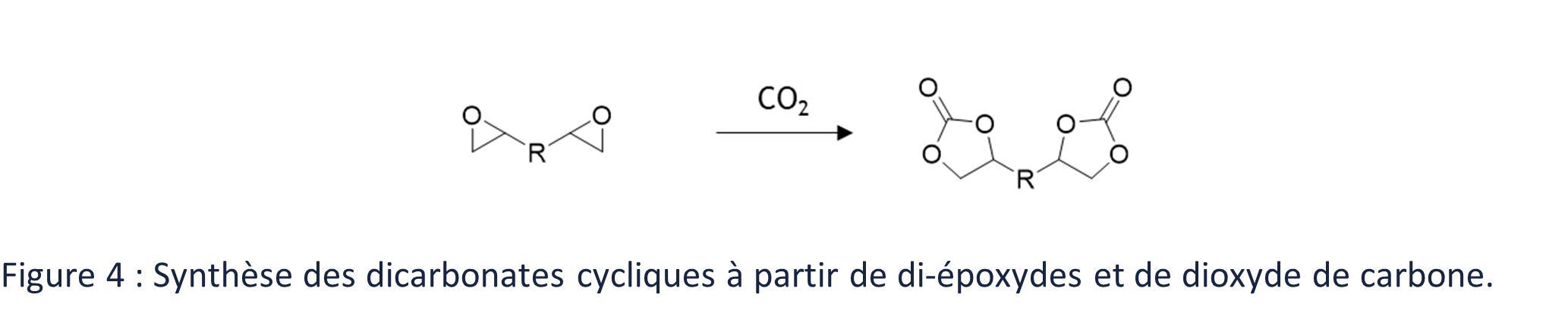
Epoxides are generated by two main routes. The 1,2-diols can be dehydrated to form the corresponding epoxides34,47,53,56 and the unsaturations can also be epoxidized. As such, triglycerides (vegetable oils) and fatty acids are substrates of interest57,5 because they have a variable number of unsaturations (between 1 and 3)15,59–6263. Many types of PHUs can thus be synthesized, both thermoplastic and thermosetting
A final synthesis route allowing access to biobased cyclic carbonates involves the cyclization of diols (Figure 5), mainly 1,2 (for 5-membered cyclic dicarbonates) but also 1,3 (for 6-membered cyclic dicarbonates)6.
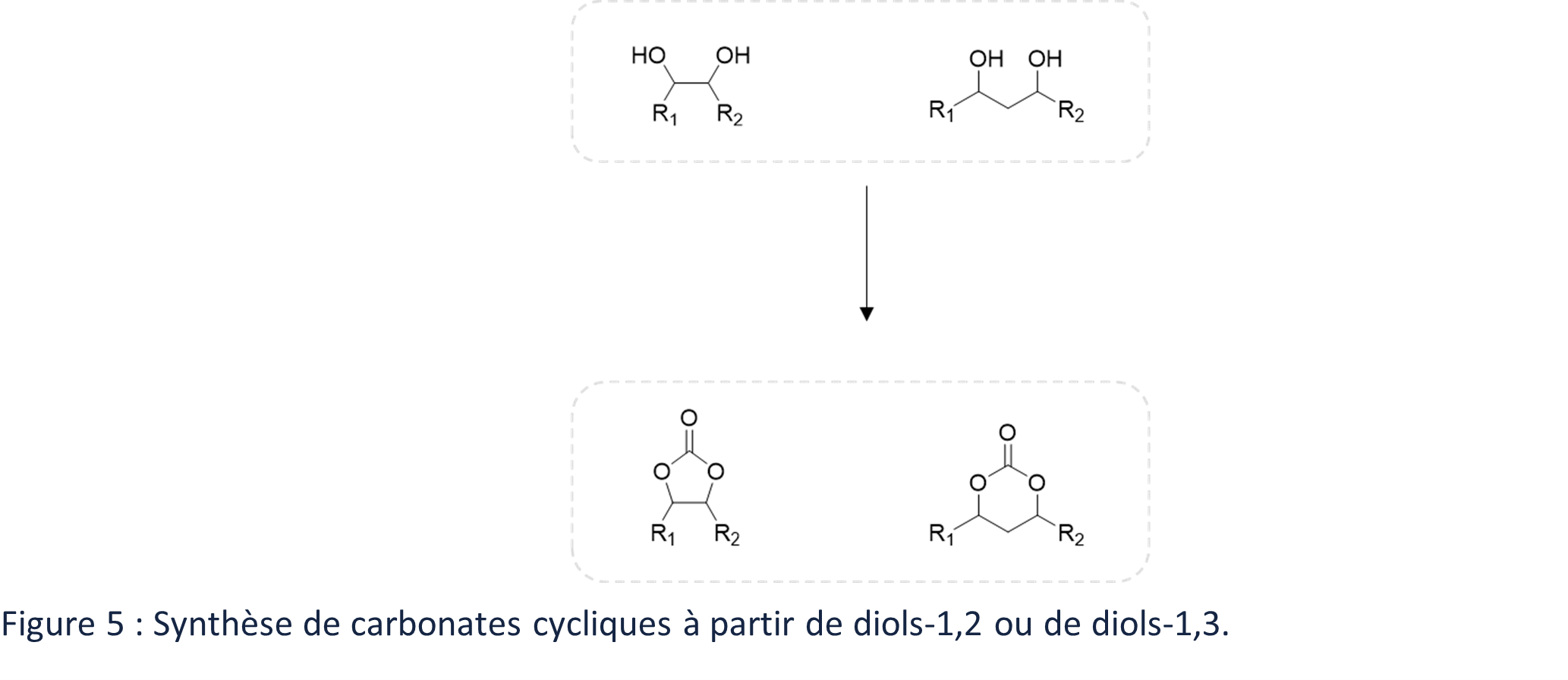
Many amines are produced by living organisms and are present in nature.64 We can cite 1,4-diaminobutane (putrescine) and its derivatives (musculamine, spermine, thermospermine, etc.),65 but also L-lysine, derived from L-aspartate, which can lead to the production of numerous diamines such as 1,5-diaminopentane (cadaverine) or homoarginine (Figure 6).66 Chitosan can also be cited, but its structure and properties make it a separate material. It is in fact a multi-amine polysaccharide of the glycosaminoglycan family (Figure 6).
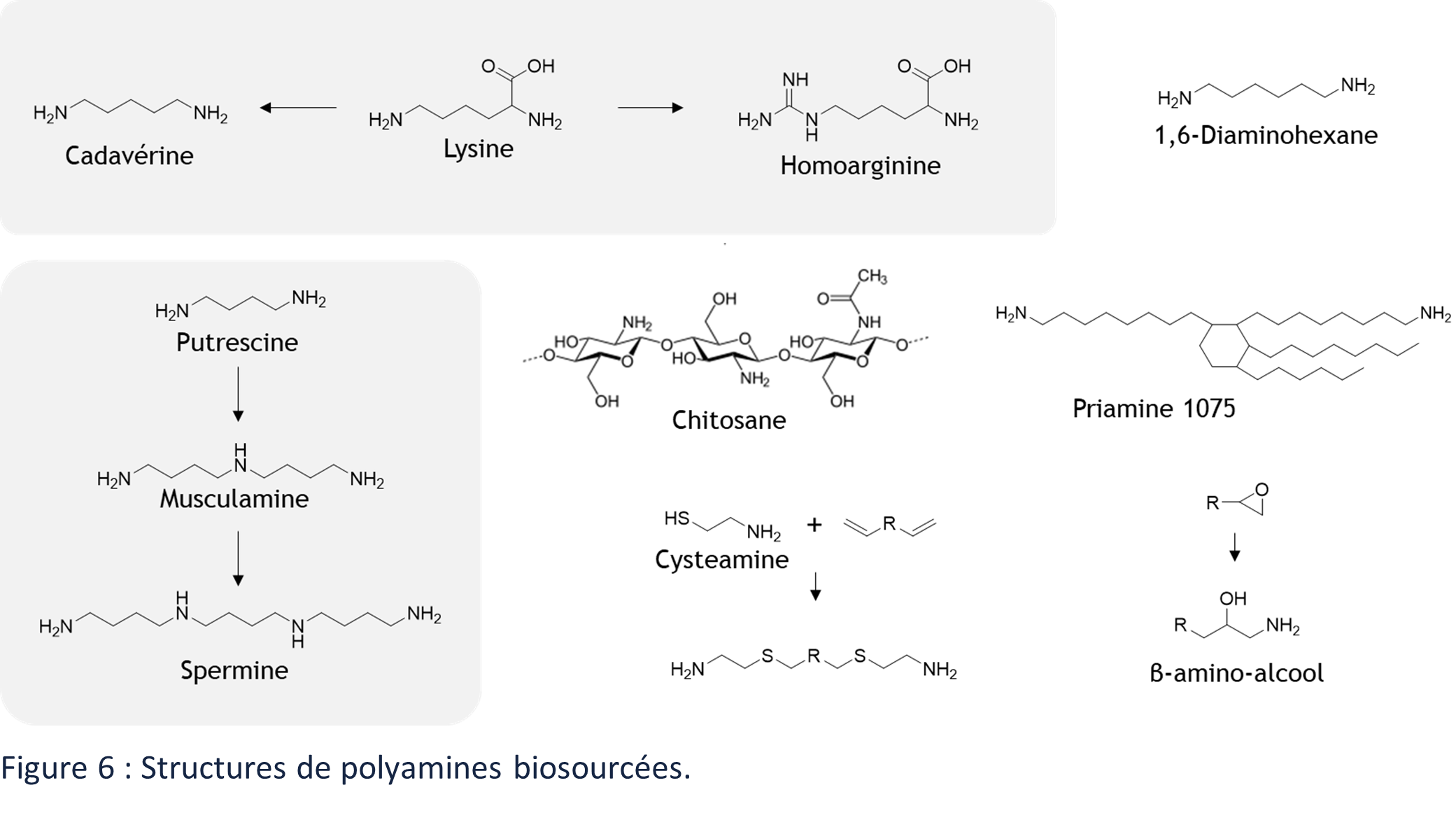
Recent reviews identify the different synthetic routes for biobased amines.6,67 Amines can be generated by various processes from bioresources but are most often derived from carboxylic acid. The polyamide industry is an important pole of synthesis of biosourced pluri-amines68 such as 1,4-diaminobutane (BASF), 1,5-diaminopentane (BAYER, Covestro, Mitsubishi Chemical), 1,10-decanediamine (Evonik) or fatty diamine marketed under the brand name PriamineTM (CRODA) (Figure 6). The amines are also widely used for the synthesis of polymers such as polyamides.
Other synthesis routes can lead to the obtention of particular pluri-amines. Epoxides lead to the obtention of β-amino alcohols by fixing ammonia on them (Figure 1. 23).69 The “click” addition of thiols, such as cysteamine, can also be used to functionalize biosourced derivatives with unsaturations (Figure 6).70,71
Research on cyclic carbonates has greatly improved their reactivity towards aminolysis and reached values close to those of their isocyanate counterpart. This reactivity can be improved thanks to two main axes: the constraint of the rings of the CCs and the introduction of electron-withdrawing groups near the ring of the CCs (Figure 7).
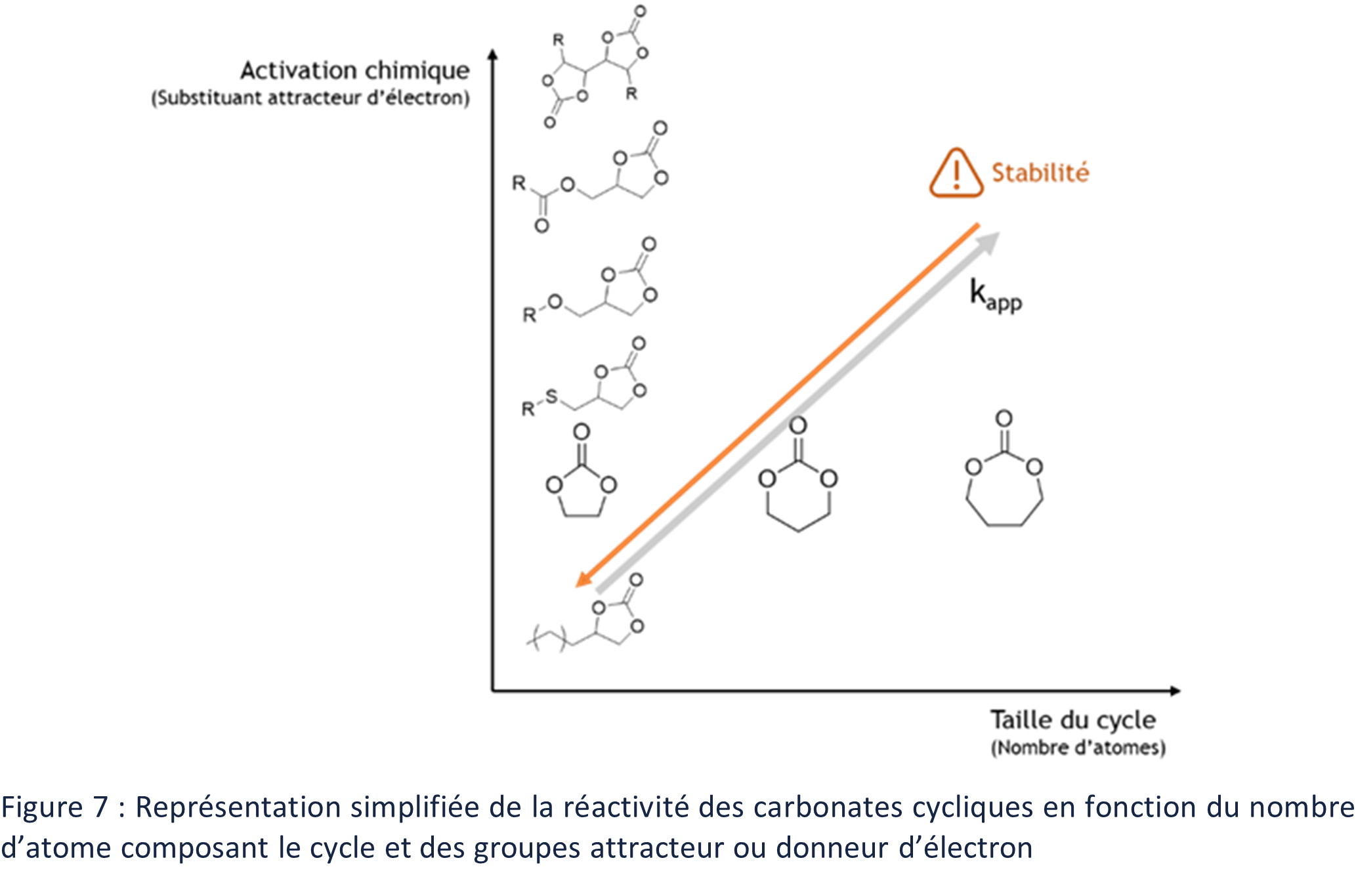
Although 5-atom CCs are the most common, 6-atom and 7-atom CCs have also been described. The reactivity of CCs with respect to the aminolysis reaction is correlated to the number of atoms composing the carbonate rings and to the increase of the ring stress. The activation energy of the aminolysis of CCs is decreased by the increasing number of atoms composing their ring and the reactivity in the presence of amines is improved. 72–74
The increase in the stress of the rings, and thus the increase in their number of atoms, has the counterpart of decreasing the stability in time of the CCs (Figure 7).75-79 The reactivity of the cyclic carbonates, and thus in particular those of the 5CCs, can however be improved thanks to the presence of electrochemical activator close to the ring of the CCs.
The presence of electron-withdrawing groups in the α, β, or γ position of cyclic carbonates results in an increase in their reactivity toward the aminolysis reaction. This chemical activation has been extensively studied over the last twenty years to improve the reactivity of CCs in the presence of amines.6,77,78,80–8 In summary, the reactivity of cyclic carbonates is increased as the activating effect of the substituent increases (Figure 7). The choice of the chemical structure of the CCs thus has an important influence on the polymerization kinetics of PHUs. Carefully chosen, the CC can therefore lead to the obtention of PHUs at low temperatures (< 80°C) in a few hours. Similarly, the kinetics of the aminolysis reaction of CCs can be further improved by the choice of amine.
Considered to be of low risk to humans and the environment, biobased CCs offer a real alternative to poly(isocyanate)s.83,84 The toxicity and corrosivity of amines is more problematic, although they are present at a certain level in living organisms.64 Indeed, it depends mainly on their chemical structure. Cyclic and aromatic amines, for example, are dangerous or even lethal, whereas some linear amines are not very dangerous. If selected and handled with care, they are generally less toxic than isocyanates and can be biobased.
PHUs are thus intended to be an alternative to polyurethanes obtained by the “isocyanate” route. However, their hydroxyurethane chemical structure differs from that of PUs and their properties are impacted by this difference.
Considérés comme peu dangereux pour l’Homme et l’environnement, les CCs biosourcés présentent une vraie alternative aux poly(isocyanate)s.83,84 La toxicité et la corrosivité des amines est plus problématique, bien que présentes à une certaine teneur chez les organismes vivants.64 En effet, elle dépend principalement de leur structure chimique. Les amines cycliques et aromatiques sont, par exemple, dangereuses voire mortelles tandis que certaines amines linéaires sont peu dangereuses. Sélectionnées et manipulées avec précaution, elles sont globalement moins toxiques que les isocyanates et peuvent être biosourcés.
The polymerization of PUs requires some precautions because isocyanates react mainly with alcohols but also with water, amines or acids (Figure 8). The aminolysis reaction of CCs presents a strong chemoselectivity. The polymerizations of PHUs can thus be carried out under less controlled conditions, with in particular the presence of water, without generating secondary reactions.
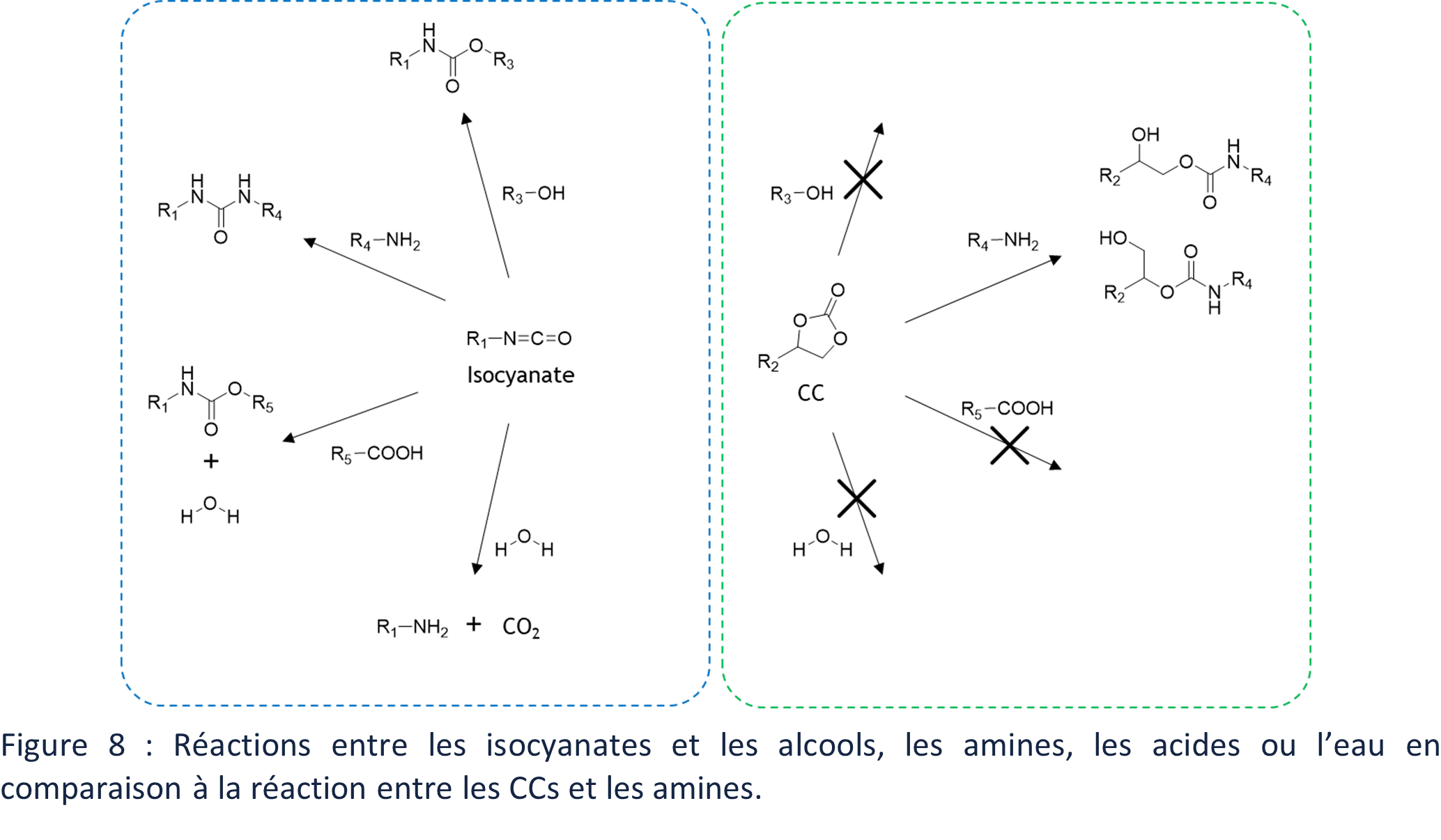
This first difference in reactivity between the monomers used for the polymerization of PUs and PHUs has a strong impact on the applications of these polymer families. Indeed, the secondary reactions of isocyanates can be condensation reactions and thus generate gases, such as CO2 in the presence of water (Figure 8). These gases are necessary and valuable for the main application of PUs, namely foam formation. PHUs cannot be used directly for this application.
The polymerization of PHUs is a little more different from that of PUs because it is a ring-opening polymerization of CCs in the presence of amine. This aminolysis of the CCs generates primary hydroxyl groups (OH)I (in position α of the urethane) or secondary hydroxyl groups (OH)II (in position β of the urethane) (Figure 9)

Although PHUS are rarely compared directly to their PUs counterpart because it is not easy to find similar CCs/amine monomer pairs to polyol/poly(isocyanate)s, the presence of hydroxyl groups along the backbone has been shown to impact the properties of PHUs compared to PUs. Thus, the thermal properties, such as glass transition and thermal degradation temperatures, of PHUs are higher than those of PUs of comparable structure.51,85 The solubility of PHU is similarly reduced in common solvents such as dichloromethane or chloroform, compared to PU. These properties are explained by the ability of the (OH)s to also interact via hydrogen bonding (Figure 10). PHUs are also sometimes presented as having better chemical resistance, especially to hydrolysis, due to the protection of the carbonyl of the urethane bond by hydroxyl groups. 8,86,87
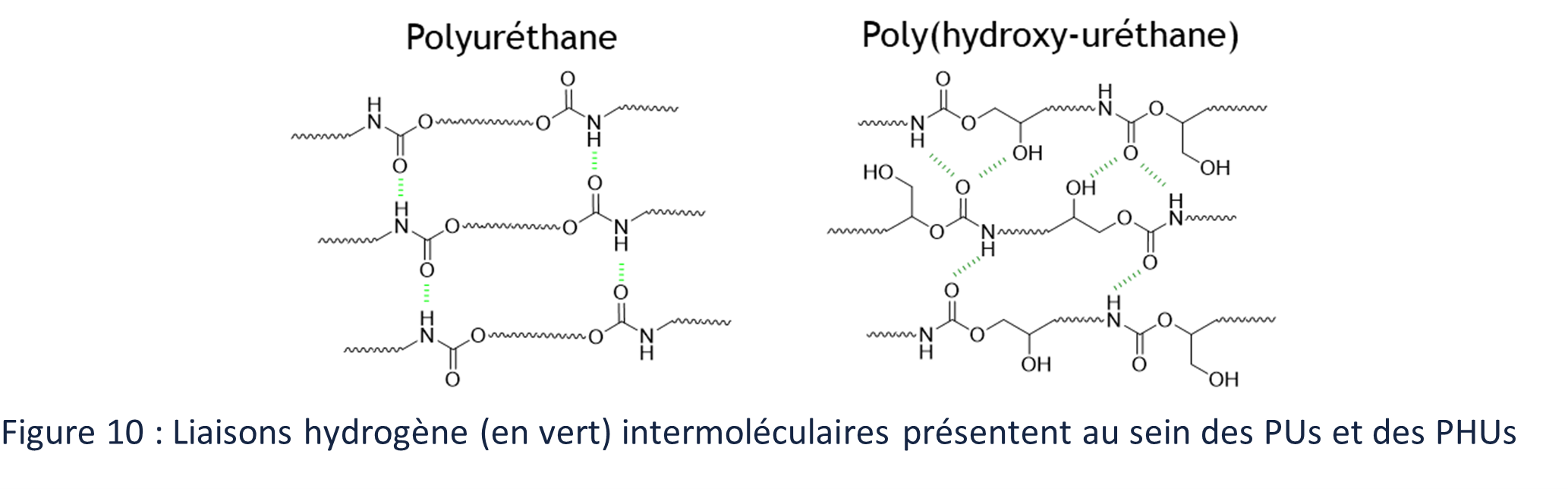
All these properties induced by (OH)s make PHUs particularly suitable for coating or adhesive type applications, as it has been very well described in two recent reviews, a second one by Gomez-Lopez et al88 and one by Khatoon et al89. PUs already exhibit excellent properties of abrasion resistance and adhesiveness, thanks in particular to the formation of micro-aggregates induced by the strong electrostatic interactions of the hydrogen bond type between the urethane bonds.90 But PHUs, also composed of urethane bonds, are all the more adapted to uses for adhesives and coatings thanks to the (OH)s. Their adhesion properties to substrates are improved compared to their Pru counterpart with similar properties.85,89,91
The fields of application of PHUs are varied. The presence of hydroxyl groups in the core of the polymer chains allows PHUs to have numerous electrostatic interactions, particularly of the hydrogen bonding type. This makes them particularly suitable for applications requiring strong substrate/polymer affinities such as coatings or adhesives. PHUs also have the property of being derived from bioresources, as we have seen, which makes them materials of the future with complementary properties to PUs.
1. Fernandez L. Global polyurethane market volume 2015-2021. Statista. Published 2021. https://www.statista.com/statistics/720341/global-polyurethane-market-size-forecast/
2. Cornille A, Auvergne R, Figovsky O, Boutevin B, Caillol S. A perspective approach to sustainable routes for non-isocyanate polyurethanes. Eur Polym J. 2017;87:535-552. doi:10.1016/j.eurpolymj.2016.11.027
3. Hicks D. A review of the global PU industry in 2016 and outlook for 2017. 2018;(February 2017).
4. Akindoyo JO, Beg MDH, Ghazali S, Islam MR, Jeyaratnam N, Yuvaraj AR. Polyurethane types, synthesis and applications-a review. RSC Adv. 2016;6(115):114453-114482. doi:10.1039/c6ra14525f
5. Kreye O, Mutlu H, Meier MAR. Sustainable routes to polyurethane precursors. Green Chem. 2013;15:1431-1455. doi:10.1039/c3gc40440d
6. Maisonneuve L, Lamarzelle O, Rix E, Grau E, Cramail H. Isocyanate-Free Routes to Polyurethanes and Poly(hydroxy Urethane)s. Chem Rev. 2015;115(22):12407-12439. doi:10.1021/acs.chemrev.5b00355
7. Delebecq E, Pascault J-P, Boutevin B, Ganachaud F. On the Versatility of Urethane/Urea Bonds: Reversibility, Blocked Isocyanate, and Non-isocyanate Polyurethane. Chem Rev. 2013;113(1):80-118. doi:10.1021/cr300195n
8. Kathalewar MS, Joshi PB, Sabnis AS, Malshe VC. Non-isocyanate polyurethanes: From chemistry to applications. RSC Adv. 2013;3:4110-4129. doi:10.1039/c2ra21938g
9. Rokicki G, Parzuchowski PG, Mazurek M. Non-isocyanate polyurethanes: Synthesis, properties, and applications. Polym Adv Technol. 2015;26(7):707-761. doi:10.1002/pat.3522
10. Figovsjy Oleg; Shapolavov, Leonid; Leykin Alexander; Birukova, Olga; Potashnikova R. Recent advances in the development of non-isocyanate polyurethanes based on cyclic carbonates. PU Mag. 2013;10(4):2-9. doi:10.1109/PPC.2013.6627453
11. Hannes B, Maria F, Moritz B, Rolf M. Isocyanate- and Phosgene-Free Routes to Polyfunctional Cyclic Carbonates and Green Polyurethanes by Fixation of Carbon Dioxide. Macromol Rapid Commun. 2014;35(14):1238-1254. doi:10.1002/marc.201400209
12. Zhang H, Liu HB, Yue JM. Organic carbonates from natural sources. Chem Rev. 2014;114(1):883-898. doi:10.1021/cr300430e
13. Wang G, Lopez L, Coile M, Chen Y, Torkelson JM, Broadbelt LJ. Identification of known and novel monomers for poly(hydroxyurethanes) from biobased materials. Ind Eng Chem Res. 2021;60(18):6814-6825. doi:10.1021/acs.iecr.0c06351
14. Helou M, Carpentier JF, Guillaume SM. Poly(carbonate-urethane): An isocyanate-free procedure from α,ω-di(cyclic carbonate) telechelic poly(trimethylene carbonate)s. Green Chem. 2011;13:266-271. doi:10.1039/c0gc00686f
15. Mokhtari C, Malek F, Manseri A, Caillol S, Negrell C. Reactive jojoba and castor oils-based cyclic carbonates for biobased polyhydroxyurethanes. Eur Polym J. 2019;113:18-28. doi:10.1016/j.eurpolymj.2019.01.039
16. Duval C, Kébir N, Jauseau R, Burel F. Organocatalytic synthesis of novel renewable non-isocyanate polyhydroxyurethanes. J Polym Sci Part A Polym Chem. 2016;54(6):758-764. doi:10.1002/pola.27908
17. Benyahya S, Habas JP, Auvergne R, Lapinte V, Caillol S. Structure-property relationships in polyhydroxyurethanes produced from terephthaloyl dicyclocarbonate with various polyamines. Polym Int. 2012;61(11):1666-1674. doi:10.1002/pi.4257
18. Carré C, Bonnet L, Avérous L. Original biobased nonisocyanate polyurethanes: Solvent- and catalyst-free synthesis, thermal properties and rheological behaviour. RSC Adv. 2014;4:54018-54025. doi:10.1039/c4ra09794g
19. Carré C, Bonnet L, Avérous L. Solvent- and catalyst-free synthesis of fully biobased nonisocyanate polyurethanes with different macromolecular architectures. RSC Adv. 2015;5(121):100390-100400. doi:10.1039/c5ra17638g
20. Magliozzi F, Chollet G, Grau E, Cramail H. Benefit of the Reactive Extrusion in the Course of Polyhydroxyurethanes Synthesis by Aminolysis of Cyclic Carbonates. ACS Sustain Chem Eng. 2019;7:17282-17292. doi:10.1021/acssuschemeng.9b04098
21. Cornille A, Blain M, Auvergne R, Andrioletti B, Boutevin B, Caillol S. A study of cyclic carbonate aminolysis at room temperature: Effect of cyclic carbonate structures and solvents on polyhydroxyurethane synthesis. Polym Chem. 2017;8(3):592-604. doi:10.1039/c6py01854h
22. Bizet B, Grau E, Cramail H, Asua JM. Volatile Organic Compound-Free Synthesis of Waterborne Poly(hydroxy urethane)–(Meth)acrylic Hybrids by Miniemulsion Polymerization. ACS Appl Polym Mater. 2020;2(9):4016-4025. doi:10.1021/acsapm.0c00657
23. Bizet B, Grau E, Cramail H, Asua JM. Crosslinked isocyanate-free poly(hydroxy urethane)s – Poly(butyl methacrylate) hybrid latexes. Eur Polym J. 2021;146(December 2020). doi:10.1016/j.eurpolymj.2020.110254
24. Quérette T, Bordes C, Sintes-Zydowicz N. Non-isocyanate polyurethane nanoprecipitation: Toward an optimized preparation of poly(hydroxy)urethane nanoparticles. Colloids Surfaces A. 2020;589:124371. doi:10.1016/j.colsurfa.2019.124371
25. Jaratrotkamjorn R, Nourry A, Pasetto P, et al. Synthesis and characterization of elastomeric, biobased, nonisocyanate polyurethane from natural rubber. J Appl Polym Sci. Published online 2017:1-12. doi:10.1002/app.45427
26. Carré C, Zoccheddu H, Delalande S, Pichon P, Avérous L. Synthesis and characterization of advanced biobased thermoplastic nonisocyanate polyurethanes, with controlled aromatic-aliphatic architectures. Eur Polym J. 2016;84:759-769. doi:10.1016/j.eurpolymj.2016.05.030
27. Anastas P, Eghbali N. Green Chemistry: Principles and Practice. Chem Soc Rev. 2010;39(1):301-312. doi:10.1039/b918763b
28. Ménard R, Caillol S, Allais F. Chemo-enzymatic synthesis and characterization of renewable thermoplastic and thermoset isocyanate-free poly(hydroxy)urethanes from ferulic acid derivatives. ACS Sustain Chem Eng. 2017;5(2):1446-1456. doi:10.1021/acssuschemeng.6b02022
29. Schimpf V, Max JB, Stolz B, Heck B, Mülhaupt R. Semicrystalline Non-Isocyanate Polyhydroxyurethanes as Thermoplastics and Thermoplastic Elastomers and Their Use in 3D Printing by Fused Filament Fabrication. Macromolecules. 2019;52(1):320-331. doi:10.1021/acs.macromol.8b01908
30. Wulf C, Reckers M, Perechodjuk A, Werner T. Catalytic Systems for the Synthesis of Biscarbonates and Their Impact on the Sequential Preparation of Non-Isocyanate Polyurethanes. ACS Sustain Chem Eng. 2020;8:1651-1658. doi:10.1021/acssuschemeng.9b06662
31. Doley S, Dolui SK. Solvent and catalyst-free synthesis of sun fl ower oil based polyurethane through non-isocyanate route and its coatings properties. Eur Polym J. 2018;102:161-168.
32. Kihara N, Endo T. Synthesis and Properties of Poly ( hydroxyurethane ) s. :2765-2773.
33. Ke J, Li X, Jiang S, et al. Promising approaches to improve the performances of hybrid non-isocyanate polyurethane. Polym Int. 2019;68(4):651-660. doi:10.1002/pi.5746
34. Nanclares J, Petrovic ZS, Javni I, Ionescu M, Jaramillo F. Segmented polyurethane elastomers by nonisocyanate route. J Appl Polym Sci. Published online 2015:7-14. doi:10.1002/app.42492
35. Gennen S, Grignard B, Thomassin JM, et al. Polyhydroxyurethane hydrogels: Synthesis and characterizations. Eur Polym J. 2016;84:849-862. doi:10.1016/j.eurpolymj.2016.07.013
36. Tomita H, Sanda F, Endo T. Structural analysis of polyhydroxyurethane obtained by polyaddition of bifunctional five-membered cyclic carbonate and diamine based on the model reaction. J Polym Sci Part A Polym Chem. 2001;39:851-859. doi:10.1002/1099-0518(20010315)39:6<851::AID-POLA1058>3.0.CO;2-3
37. Steblyanko A, Choi W, Sanda F, Endo T. Addition of Five-Membered Cyclic Carbonate with Amine and Its Application to Polymer Synthesis. J Polym Sci Part A Polym Chem. 2000;38:2375-2380.
38. Sukumaran Nair A, Cherian S, Balachandran N, Panicker UG, Kalamblayil Sankaranarayanan SK. Hybrid Poly(hydroxy urethane)s: Folded-Sheet Morphology and Thermoreversible Adhesion. ACS Omega. 2019;4(8):13042-13051. doi:10.1021/acsomega.9b00789
39. Ochiai B, Inoue S, Endo T. One-pot non-isocyanate synthesis of polyurethanes from bisepoxide, carbon dioxide, and diamine. J Polym Sci Part A Polym Chem. 2005;43(24):6613-6618. doi:10.1002/pola.21103
40. Lombardo VM, Dhulst EA, Leitsch EK, et al. Cooperative catalysis of cyclic carbonate ring opening: Application towards non-isocyanate polyurethane materials. European J Org Chem. Published online 2015:2791-2795. doi:10.1002/ejoc.201500313
41. Beniah G, Liu K, Heath WH, Miller MD, Scheidt KA, Torkelson JM. Novel thermoplastic polyhydroxyurethane elastomers as effective damping materials over broad temperature ranges. Eur Polym J. 2016;84:770-783. doi:10.1016/j.eurpolymj.2016.05.031
42. Beniah G, Chen X, Uno BE, et al. Combined Effects of Carbonate and Soft-Segment Molecular Structures on the Nanophase Separation and Properties of Segmented Polyhydroxyurethane. Macromolecules. 2017;50(8):3193-3203. doi:10.1021/acs.macromol.6b02513
43. Leitsch EK, Beniah G, Liu K, et al. Nonisocyanate Thermoplastic Polyhydroxyurethane Elastomers via Cyclic Carbonate Aminolysis: Critical Role of Hydroxyl Groups in Controlling Nanophase Separation. ACS Macro Lett. 2016;5:424-429. doi:10.1021/acsmacrolett.6b00102
44. Beniah G, Fortman DJ, Heath WH, Dichtel WR, Torkelson JM. Non-Isocyanate Polyurethane Thermoplastic Elastomer: Amide-Based Chain Extender Yields Enhanced Nanophase Separation and Properties in Polyhydroxyurethane. Macromolecules. 2017;50:4425-4434. doi:10.1021/acs.macromol.7b00765
45. Beniah G, Uno BE, Lan T, et al. Tuning nanophase separation behavior in segmented polyhydroxyurethane via judicious choice of soft segment. Polymer (Guildf). 2017;110:218-227. doi:10.1016/j.polymer.2017.01.017
46. Beniah G, Heath WH, Torkelson JM. Functionalization of hydroxyl groups in segmented polyhydroxyurethane eliminates nanophase separation. J Polym Sci Part A Polym Chem. 2017;55:3347-3351. doi:10.1002/pola.28722
47. Ma Z, Li C, Fan H, Wan J, Luo Y, Li BG. Polyhydroxyurethanes (PHUs) Derived from Diphenolic Acid and Carbon Dioxide and Their Application in Solvent- and Water-Borne PHU Coatings. Ind Eng Chem Res. 2017;56:14089-14100. doi:10.1021/acs.iecr.7b04029
48. Maisonneuve L, More AS, Foltran S, et al. Novel green fatty acid-based bis-cyclic carbonates for the synthesis of isocyanate-free poly(hydroxyurethane amide)s. RSC Adv. 2014;4:25795-25803. doi:10.1039/c4ra03675a
49. Arunachalam R, Chinnaraja E, Subramanian S, Suresh E, Subramanian PS. Catalytic Conversion of Carbon Dioxide Using Binuclear Double-Stranded Helicates: Cyclic Carbonate from Epoxides and Diol. ACS Omega. 2020;5(25):14890-14899. doi:10.1021/acsomega.9b04241
50. North M, Pasquale R. Mechanism of cyclic carbonate synthesis from epoxides and CO2. Angew Chemie – Int Ed. 2009;48(16):2946-2948. doi:10.1002/anie.200805451
51. Kihara N, Endo T. Synthesis and Properties of Poly (hydroxyurethane)s. J Polym Sci Part A Polym Chem. 1993;31:2765-2773.
52. Steblyanko A, Choi W, Sanda F, Endo T. Addition of five-membered cyclic carbonate with amine and its application to polymer synthesis. J Polym Sci Part A Polym Chem. 2000;38(13):2375-2380. doi:10.1002/1099-0518(20000701)38:13<2375::AID-POLA100>3.0.CO;2-U
53. BROCAS A-L, CENDEJAS G, CAILLOL S, DEFFIEUX A, CARLOTTI S. Controlled Synthesis of Polyepichlorohydrin with Pendant Cyclic Carbonate Functions for Isocyanate-Free Polyurethane Networks. J Polym Sci Part A Polym Chem. 2011;49:2677–2684. doi:10.1002/pola
54. Guillame SM, Khalil H, Misra M. Green and sustainable polyurethanes for advanced applications. J Appl Polym Sci. 2017;134(45). doi:10.1002/app.45646
55. Zareanshahraki F, Asemani HR, Skuza J, Mannari V. Synthesis of non-isocyanate polyurethanes and their application in radiation-curable aerospace coatings. Prog Org Coatings. 2020;138(September 2019):105394. doi:10.1016/j.porgcoat.2019.105394
56. Auvergne R, Caillol S, David G, Boutevin B, Pascault JP. Biobased thermosetting epoxy: Present and future. Chem Rev. 2014;114(2):1082-1115. doi:10.1021/cr3001274
57. Lee DS, Noh BS, Bae SY, Kim K. Characterization of fatty acids composition in vegetable oils by gas chromatography and chemometrics. Anal Chim Acta. 1998;358(2):163-175. doi:10.1016/S0003-2670(97)00574-6
58. Kim J, Kim DN, Lee SH, Yoo SH, Lee S. Correlation of fatty acid composition of vegetable oils with rheological behaviour and oil uptake. Food Chem. 2010;118(2):398-402. doi:10.1016/j.foodchem.2009.05.011
59. Yu AZ, Setien RA, Sahouani JM, Docken J, Webster DC. Catalyzed non-isocyanate polyurethane (NIPU) coatings from bio-based poly(cyclic carbonates). J Coatings Technol Res. 2018;16(1):41-57. doi:10.1007/s11998-018-0135-7
60. Poussard L, Mariage J, Grignard B, et al. Non-Isocyanate Polyurethanes from Carbonated Soybean Oil Using Monomeric or Oligomeric Diamines to Achieve Thermosets or Thermoplastics. Macromolecules. 2016;49(6):2162-2171. doi:10.1021/acs.macromol.5b02467
61. Tan SG, Chow WS. Biobased epoxidized vegetable oils and its greener epoxy blends: A review. Polym – Plast Technol Eng. 2010;49(15):1581-1590. doi:10.1080/03602559.2010.512338
62. Laprise CM, Hawboldt KA, Kerton FM, Kozak CM. Synthesis of a Renewable, Waste-Derived Nonisocyanate Polyurethane from Fish Processing Discards and Cashew Nutshell-Derived Amines. Macromol Rapid Commun. 2021;42(3):1-5. doi:10.1002/marc.202000339
63. Johns A, Gibbons L, Smith M, Edwards K, Quirino RL. Plant Oil-based Polyhydroxyurethanes. In: Madbouly SA, Zhang C, Kessler MR, eds. Bio-Based Plant Oil Polymers and Composites. Elsevier; 2016:55-70.
64. Pegg AE. Toxicity of polyamines and their metabolic products. Chem Res Toxicol. 2013;26(12):1782-1800. doi:10.1021/tx400316s
65. Bitrián M, Zarza X, Altabella T, Tiburcio AF, Alcázar R. Polyamines under abiotic stress: Metabolic crossroads and hormonal crosstalks in plants. Metabolites. 2012;2(3):516-528. doi:10.3390/metabo2030516
66. Jancewicz AL, Gibbs NM, Masson PH. Cadaverine’s functional role in plant development and environmental response. Front Plant Sci. 2016;7(June):1-8. doi:10.3389/fpls.2016.00870
67. Froidevaux V, Negrell C, Caillol S, Pascault JP, Boutevin B. Biobased Amines: From Synthesis to Polymers; Present and Future. Chem Rev. 2016;116(22):14181-14224. doi:10.1021/acs.chemrev.6b00486
68. De Jong E, Stichnothe H, Bell G, Jorgensen H. Bio-Based Chemicals: A 2020 Update.; 2020. https://task42.ieabioenergy.com/wp-content/uploads/sites/10/2020/02/Bio-based-chemicals-a-2020-update-final-200213.pdf
69. Blattmann H, Mülhaupt R. Multifunctional β-amino alcohols as bio-based amine curing agents for the isocyanate- and phosgene-free synthesis of 100% bio-based polyhydroxyurethane thermosets. Green Chem. 2016;18(8):2406-2415. doi:10.1039/c5gc02563j
70. Fache M, Darroman E, Besse V, Auvergne R, Caillol S, Boutevin B. Vanillin, a promising biobased building-block for monomer synthesis. Green Chem. 2014;16(4):1987-1998. doi:10.1039/c3gc42613k
71. Darroman E, Auvergne R, Boutevin B, Caillol S, Equipe IAM. New aromatic amine based on cardanol giving new biobased epoxy networks with cardanol†. Eur J Lipid Sci Technol. Published online 2014.
72. Yuen A, Bossion A, Bengoa EG-, et al. Room temperature synthesis of non‐isocyanate polyurethanes (NIPUs) using highly reactive N‐substituted 8‐membered cyclic carbonates. Polym Chem. 2016;7(11):2105-2111.
73. Tomita H, Sanda F, Endo T. Polyaddition of bis(seven-membered cyclic carbonate) with diamines: A novel and efficient synthetic method for polyhydroxyurethanes. J Polym Sci Part A Polym Chem. 2001;39(23):4091-4100. doi:10.1002/pola.10058
74. Tomita H, Sanda F, Endo T. Polyaddition Behavior of bis ( Five- and Six-Membered Cyclic Carbonate ) s with Diamine. Published online 2000:860-867.
75. He Y, Keul H, Möller M. Synthesis, characterization, and application of a bifunctional coupler containing a five- and a six-membered ring carbonate. React Funct Polym. 2011;71(2):175-186. doi:10.1016/j.reactfunctpolym.2010.11.031
76. Besse V, Foyer G, Auvergne R, Caillol S, Boutevin B. Access to nonisocyanate poly(thio)urethanes: A comparative study. J Polym Sci Part A Polym Chem. 2013;51:3284-3296. doi:10.1002/pola.26722
77. Lamarzelle O, Durand PL, Wirotius AL, Chollet G, Grau E, Cramail H. Activated lipidic cyclic carbonates for non-isocyanate polyurethane synthesis. Polym Chem. 2016;7(7):1439-1451. doi:10.1039/c5py01964h
78. Cornille A, Blain M, Auvergne R, Andrioletti B, Boutevin B, Caillol S. A study of cyclic carbonate aminolysis at room temperature: Effect of cyclic carbonate structures and solvents on polyhydroxyurethane synthesis. Polym Chem. Published online 2017:592-604. doi:10.1039/c6py01854h
79. Maisonneuve L, Wirotius AL, Alfos C, Grau E, Cramail H. Fatty acid-based (bis) 6-membered cyclic carbonates as efficient isocyanate free poly(hydroxyurethane) precursors. Polym Chem. 2014;5:6142-6147. doi:10.1039/c4py00922c
80. Tomita H, Sanda F, Endo T. Model reaction for the synthesis of polyhydroxyurethanes from cyclic carbonates with amines: Substituent effect on the reactivity and selectivity of ring-opening direction in the reaction of five-membered cyclic carbonates with amine. J Polym Sci Part A Polym Chem. 2001;39(21):3678-3685. doi:10.1002/pola.10009
81. Garipov RM, Sysoev VA, Mikheev V V., et al. Reactivity of Cyclocarbonate Groups in Modified Epoxy–Amine Compositions. Dokl Phys Chem. 2003;393:289-292. doi:10.1023/B
82. Goldstein BN, Goryunov AN, Gotlib YY, et al. Investigation of cooperative kinetics on reactions of functional groups on polymer chains. J Polym Sci Part A-2 Polym Phys. 1971;9(5):769-777. doi:10.1002/pol.1971.160090501
83. Schäffner B, Schäffner F, Verevkin SP, Börner A. Organic carbonates as solvents in synthesis and catalysis. Chem Rev. 2010;110(8):4554-4581. doi:10.1021/cr900393d
84. Lopes EJC, Ribeiro APC, Martins LMDRS. New Trends in the Conversion of CO2 to Cyclic Carbonates. Catalysts. 2020;10(479). doi:10.1016/b978-0-12-433804-3.50012-3
85. Leitsch EK, Heath WH, Torkelson JM. Polyurethane/polyhydroxyurethane hybrid polymers and their applications as adhesive bonding agents. Int J Adhes Adhes. 2016;64:1-8. doi:10.1016/j.ijadhadh.2015.09.001
86. Datir PR. A novel cyclocarbonate based technology for isocyanate free polyurethane. Published online 2007.
87. Pouladi J, Mirabedini SM, Eivaz Mohammadloo H, Rad NG. Synthesis of novel plant oil-based isocyanate-free urethane coatings and study of their anti-corrosion properties. Eur Polym J. 2021;153(April):110502. doi:10.1016/j.eurpolymj.2021.110502
88. Gomez-Lopez A, Panchireddy S, Grignard B, et al. Poly(hydroxyurethane) Adhesives and Coatings: State-of-the-Art and Future Directions. ACS Sustain Chem Eng. 2021;9(29):9541-9562. doi:10.1021/acssuschemeng.1c02558
89. Khatoon H, Iqbal S, Irfan M, Darda A, Rawat NK. A review on the production, properties and applications of non-isocyanate polyurethane: A greener perspective. Prog Org Coatings. 2021;154(February):106124. doi:10.1016/j.porgcoat.2020.106124
90. Szycher M. Polyurethane Adhesives. In: Szycher’s Handbook of Polyurethanes. Szycher, M. Taylor and Francis Group: Boca Raton; 2013:393−416.
91. Llevot A, Meier M. Perspective: green polyurethane synthesis for coating applications. Polym Int. 2019;68(5):826-831. doi:10.1002/pi.5655