The medical device industry which produces a large number of products (from surgical gloves to artificial joints to imaging devices), driven by innovation and new technologies, has become one of the largest markets in the healthcare sector.[1] The explosion in the sophistication and application of devices makes it possible to help improve human health in ways unimaginable just a few years ago.
All of these devices are intended to be used in the treatment, mitigation, diagnosis and/or prevention of diseases and abnormal physical conditions, but all are manufactured from non-natural materials, e.g. silicone, latex rubber, metals, ceramics, synthetic plastics, etc. and are often hydrophobic and non-slippery.
The introduction of foreign objects into the patient’s body may not only cause pain and discomfort but also increase the risk of injury, infection, and even life-threatening and therefore friction-reducing surface-modification using lubricious polymer coating technologies has been used for decades to facilitate the insertion and placement of devices (e.g. stents, catheters, bioabsorbable scaffolds, guidewires and other products) within the body. Ophthalmology is another area where such coatings have proven extremely beneficial – in the delivery of intraocular lenses, for example, as the delivery cartridges used to place the lenses must employ slippery surfaces to reduce damage.
Based on the wettability and water contact angles, lubricious coatings may be classified into two main categories, hydrophilic coating and hydrophobic coating. Two extreme terms may be applied when it is necessary to make a distinction, superhydrophilic coating and superhydrophobic coating.
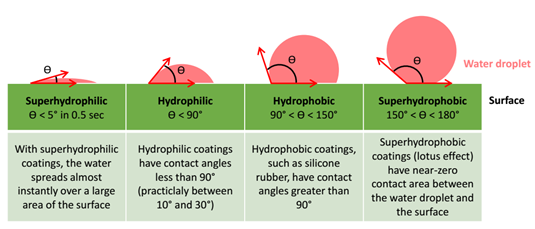
Depending on the specific design and performance requirements of the device, one coating technology may outperform another in terms of application and efficiency.
Hydrophilic coating technologies by using appropriate hydrophilic polymers which are polar and ionic, are able to absorb water and become slippery in aqueous environments and thus have low coefficients of friction, deliver lubricious, abrasion resistant, non-thrombogenic, and biocompatible surfaces; whilst hydrophobic coatings use nonpolar, water repellent molecules (or do not absorb water) and are thus less slippery than hydrophilic coatings in aqueous media.
Hydrophilic coating technologies creating water-attracting surfaces make polymeric devices fluid-responsive by either physically depositing lubricious polymers on the surface or by chemically grafting hydrophilic polymers onto the surface via covalent bonds. In order to enhance the adhesion of coating layer on substrate surface, several activation techniques, e.g. heat, UV, plasma or coronal treatments will normally be applied. Chemical bonding is a key to improve the durability as well as prevent delamination of hydrophilic coating from coated surfaces. The lubricity and water retention properties of hydrophilic coatings reduce the force required to manipulate endovascular medical devices during interventional procedures. They can minimize the friction between coated devices and tissues up to 100 times as compared to uncoated surface. This dramatically helps reduce the risk of damage to blood vessel walls, prevent vasospasm, and allow navigation in tortuous vascular pathways and lesions inaccessible. Besides, hydrophilic coatings on medical devices can create an interface that the human immune system does not recognize as artificial, significantly reducing the risk of multi-problems.[2]
For devices and instruments that become fouled with fluids or tissue debris, hydrophobic coatings show a super performance in keeping surgical tools cleaner thanks to its repellency to fluids, which makes blood, urine, or tissue sheets slide off easily, as well as reduces risks of contamination and infections in patients.[3]
Although there are numerous benefits of using lubricious coatings for medical device applications, they do have some drawbacks. One of these challenges is the separation of the polymer coat during an interventional procedure. This delamination occurs when the coating integrity or chemical bond holding the polymer coat to the surface or base coat layer is weak. The physical/chemical bonds break, causing the polymer coat to delaminate and “flake” or “peel” away from the device and enter the bloodstream.[4]
When it comes to lubricious coatings, device designers have a wide range of synthetic and naturally polymeric materials to choose from in order to incorporate into their coating formulations, as well as various technologies for their strong and durable adhesion to the substrate, for examples :
- Biocompatibility
- Toxicity
- Lubricity
- Durability
- Sterilizability
- Coating thickness
- Hydration rate
- etc.
The method to apply the coating is equally as important as the nature of the coating materials, and each method has its own advantages and disadvantages. It is important to note that not all methods are applicable to all devices or materials. Lubricious coatings are usually applied to the exterior surfaces of devices by dipping, spray painting, spin coating, wiping, etc. followed by UV or heat curing. Applying a coating to the inner lumen of a catheter is much more complicated and challenging.
Dip coating is a common technique for coating medical devices and involves different steps : 1) surface preparation, e.g. washing, plasma, corona, etc.; 2) submersion of the device in a liquid coating formulation; 3) withdrawal from the coating liquid; 4) drying and/or curing via UV or heat; 5) postprocessing.
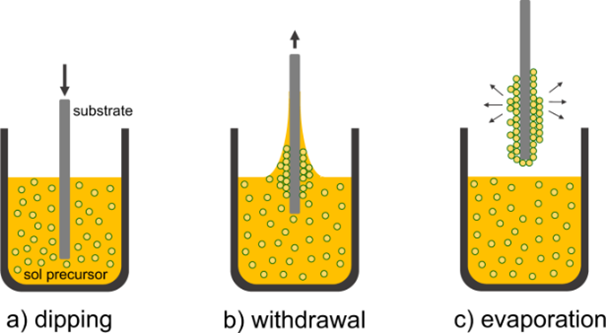
Spray coating uses a nozzle and controller to spray a coating solution onto the surface as a mist. Ultrasonic transducers may be used to control spray droplet size, which affects the thickness and quality of the coating.
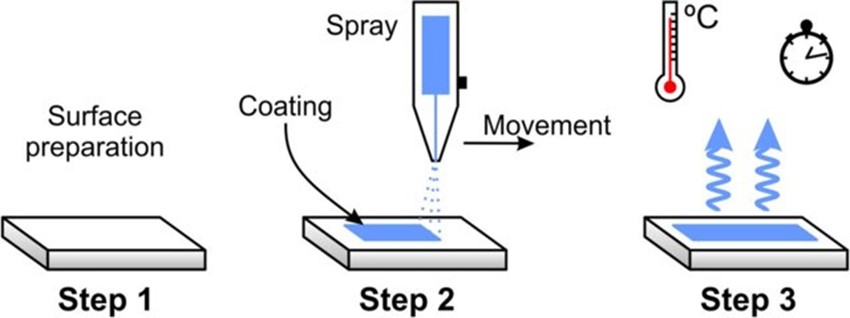
Spin coating is another technique to apply thin films to substrates. The process is quick and easy to produce homogeneous films (from a few nanometers to several microns in thickness); however, it can only be used for flat surfaces.
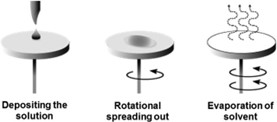
A successful story of super lubricious polymer introduced into the medical device coating market is the use of hydrophilic polyurethane, ExpertSurf. More information of ExpertSurf technology can be found on our dedicated page
Meanwhile, PolymerExpert is in progress of development of a new class of lubricious polymer, BzGliss, based on PVP with the integration of photo-crosslinking functional groups which is believed to enhance the durability of the hydrophilic coating and possibility to apply on diverse substrate materials.
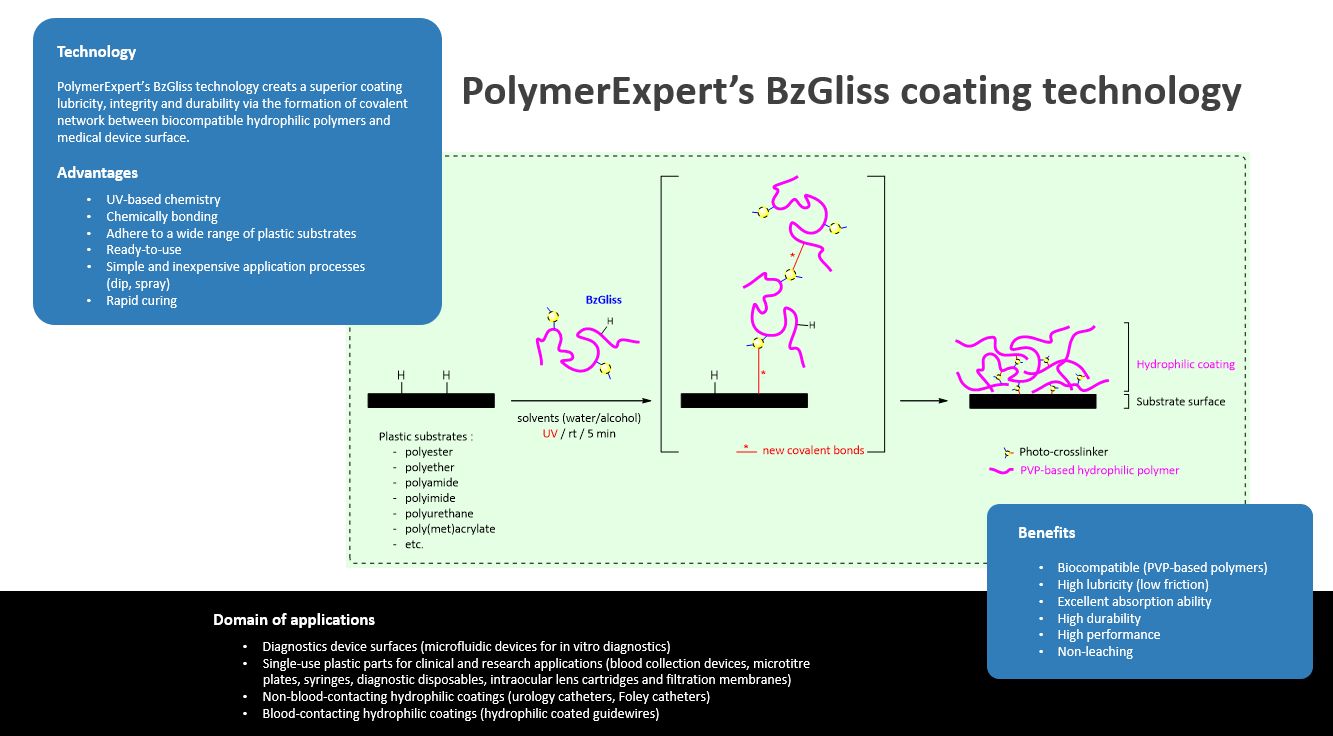
References [1] The global medical devices market size was valued at $489 billion in 2021 and is projected to grow to $719 billion by 2029. While the global medical coatings market size was valued at $4 billion in 2021 and is projected to grow to $8 billion by 2029. (https://www.fortunebusinessinsights.com/industry-reports/medical-devices-market-100085 and https://www.fortunebusinessinsights.com/medical-coatings-market-104536) [2] Some examples of hydrophilic polymers : polyethylene oxide, polyacrylic acid, polyacrylamides, poly(sodium-4-styrenesulfonates), poly(3-hydroxybutyric acids), polyvinylpyrrolidones, 2-hydroxyethyl methacrylates, hydrophilic polyurethanes, etc. Hydrophilic polyurethanes (e.g. ExpertSurf) which have high water absorbency being capable of absorbing anywhere from about 500% to about 2000% water by weight, may also be used for the lubricious coating either alone or in combination with hydrophilic polymers. These polymers may be advantageously blended with polyurethanes having lesser water absorbency. [3] Some examples of hydrophobic polymers include silicones (e.g. organosiloxane polymers), functionalized silicones, hydrolyzable silanes which form silicones, fluorosilanes and other fluoropolymers, cellulose esters and ethers, ethyl cellulose, cellulose nitrate, cellulose acetate, cellulose acetate butyrate, cellulose acetate propionate, hydrophobic polyurethanes, polyacrylates, natural and synthetic elastomers, polyacetals, hydrophobic polyamides, polyvinylidene chloride, polycarbonate, homopolymers and copolymers of vinyl compounds, polyvinylchloride, glycerin, olive, vegetable, and other natural oils. [4] Cardiovasc. Pathol. 2017, 45-54 [5] J. Sol-Gel Sci. Technol. 2022, 125-141 [6] Environ. Sci. Pollut. Res. 2021, 23610-23633 [7] IRBM 2018, 268-278