It is customary to distinguish four major classes of materials:
- metals and their alloys;
- ceramics and glass;
- polymers;
- composite.
Among these classes, three of them can have a shape memory function: alloys, polymers and composite materials.
Shape memory alloy, widely used in everyday life, have been studied for longer than shape memory polymers. These two groups of smart materials have very different physical, mechanical, thermal and electrical properties. The mechanism behind the shape memory effect of AMFs is the crystallographic phases, called martensitic and austenitic phases by analogy with steel. The transition from one phase to the other is done either by a change in temperature or by the application of a constraint.
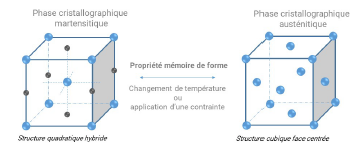
The phase transformation of SMAs has several interests:
- Low displacement of atoms (chemical composition remains unchanged even locally);
- Iso volume ;
- Reversible.
Alloys with shape memory properties are: certain brasses, certain copper-aluminum alloys and nickel-titanium, commonly called nitinol. They are used, especially in orthodontics for dental straightening. Their mechanical characteristics are sufficiently important to ensure the arrangement of the teeth.
Polymers, commonly known as “plastics”, have imposed themselves in all fields. Used from the most common objects to the most sophisticated applications, their properties depend on the arrangement of the molecular chains constituting them. We distinguish :
– thermoplastics ;
– elastomers ;
– thermosets.
- Thermoplastic polymers are “recyclable”. They are made up of linear or ramified macromolecules. Cohesion between the molecular chains is provided by low-energy Van der Waals bonds. Some of these polymers are semi crystalline, they contain then amorphous zones and ordered crystalline regions.
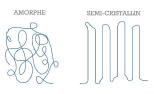
- Elastomers are amorphous materials. They are made up of linear macromolecules linked together by a few bridges between their chains. The chemical reaction leading to these links between chains is called vulcanization and allows a cross-linking of the
- Thermoset polymers are amorphous and are formed by a three-dimensional network of macromolecules. They are cross-linked, the cross-linking rate being 10 to 100 times higher than in elastomers.
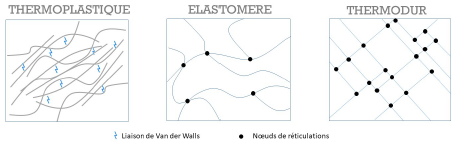
During a temperature change, a polymer can pass through four structural state domains delimited by three specific temperatures:
– the glass transition temperature Tg, this transition being observed in the amorphous phase of the polymer,
– the melting temperature Tm which concerns only the crystalline phase of the polymer if it exists,
– the thermal decomposition temperature Td where the polymer loses its integrity.
The mechanical properties of polymers vary according to their temperature, which gives them a “shape memory”.
The shape memory effect is the ability for a material to be deformed in a stable manner within a certain temperature range and to return to its original shape under the action of an external stimulus. Several stimuli can be used to activate the shape memory of a polymer: water, heat, ultraviolet light, electricity, etc.
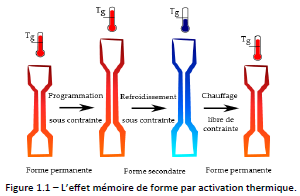
Figure 1.1 shows the shape memory effect of a polymer responding to a thermal stimulus: the most used activation to date.
The first step is the “programming” of the material: it consists in mechanically deforming it under heat (T > Tg) until the desired secondary shape is obtained. During the second step, the material is cooled, while maintaining the applied force. Then, the constraint are released, resulting in a slight springback of the material. At this point, if no heat treatment is applied, the secondary shape is retained. Finally, the initial, or permanent, shape is restored by heating the material free of external forces. The temperature above which the material must be heated to fix the secondary shape and regain the permanent shape is within the transition range of the material (T>Tg).
The shape memory effect is more or less interesting depending on the class of polymers studied. They have been classified, focusing on the chemical bonds between the molecules, to obtain 4 categories:
- 1. The thermosetting, glassy, covalently cross-linked network
This class of polymers has a wide range of glass transition temperatures that can be adjusted depending on the monomer making up the polymer chain. It is possible to change the mechanical properties of these polymers by modifying the extent of cross-linking and the glass transition temperature. This plays an important role in determining their final application. Although they have an excellent shape recovery capacity, these polymers, once processed, are difficult to reshape. However, due to their wide Tg range and adjustable modulus, these polymers have advantages over the other classes described below.The shape memory effect specific to thermoset polymers
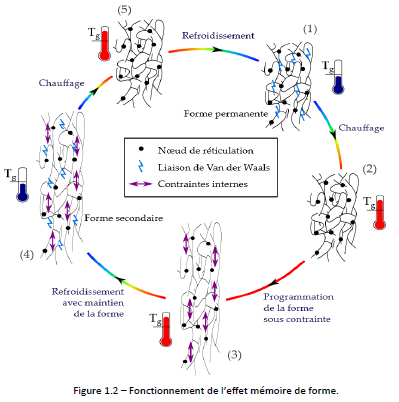
Figure 1.2 explains how the shape memory of a thermoset polymer works. In its permanent form at room temperature in phase (1), the rigidity of the polymer is provided by Van der Waals bonds. By heating (2), these bonds disappear and allow the mobility of the chains within the limit of the cross-linking nodes (the elongation of the material will be all the higher as the length of the chains between cross-linking nodes is large). The polymer can therefore be deformed (3). Internal constraint appear because the conformation of the molecules no longer corresponds to their stable state. By maintaining the deformation and cooling (4), the Van der Waals bonds reform and maintain the polymer in the secondary form. Upon heating, the Van der Waals bonds break, and the polymer returns to its permanent shape due to internal constraint.
This shape memory of polymers has been known for several decades, but in the last few years, it has been the subject of renewed interest in the world of research, as well as in industrial circles, because many innovative applications are possible. (Cf IV. Applications of shape memory polymers).
- 2. The semi-crystalline, covalently cross-linked network
In this class of SMPs, in addition to the glass transition temperature (Tg), the melting temperature (Tm) of the semi-crystalline networks can also be used to trigger shape recovery behavior. These polymers are easy to work with below their critical temperatures (Tg and Tm). Shape recovery rates are faster than those observed in glassy thermoset materials. However, like glassy thermoset polymers, they are difficult to reshape once processed. In addition, their rigidity depends on the degree of crystallinity and thus indirectly on the extent of cross-linking. This gives the possibility to have a flexible modulus and a fast shape recovery. This class of materials includes; semi-crystalline rubbers and liquid crystal elastomers. Although they have faster shape recovery rates, they lack thermal stability. - 3. The glassy, physically cross-linked copolymer
Special methods have been developed for the manufacture of polymers belonging to this class of physically cross-linked glassy copolymers. In this SMP group, the soft and hard fractions of thermoplastics form physical cross-links that give super elasticity, as well as Tg, which promote shape memory behavior. The characteristic of materials in this class is that when subjected to a temperature above the glass transition (Tg) and melting temperature (Tm), the polymer flows and can be processed to a new shape. This processing capability is possible because they are only physically cross-linked, and have a stiffness similar to cross-linked glassy thermosets. - 4. The physically cross-linked semi-crystalline block copolymer
The characteristic of this class of polymers involves the use of the melting temperature (Tm) of block copolymers to trigger shape recovery. For these polymers, the soft domain crystallizes. Thus, instead of their Tg, the Tm could be used to activate the polymer and the temporary shape is thus fixed when the soft segments crystallize. This material can be processed above its melting temperature and its rubbery properties could be adjusted by varying the soft segment/hard segment ratio. In addition, the transition temperature can be controlled by modifying the soft segments. Finally, these polymers can be biodegradable and biocompatible.
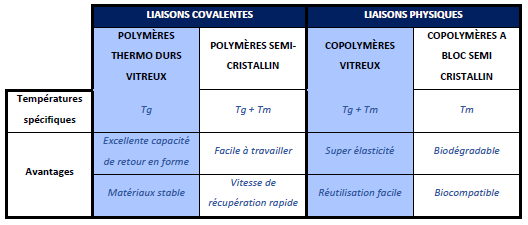
The materials with the most interesting properties are the thermoset polymers. PolymerExpert works specifically with this type of material but can also develop SMPs with other properties.
When compared to alloys and shape memory polymers, the latter exhibit high elastic strain (about 200%), significant recoverable constraint, low cost, low density, ease of processing, and a wide range of adjustable properties such as stiffness and transition temperature. Although SMPs have many advantages, the difference in modulus is notable when compared to SMAs. Furthermore, this modulus decreases as the polymer transitions into the rubbery phase (soft domain). They are also incapable of reversible transformation into shape memory alloys. A comparison of their properties is presented in the table below.
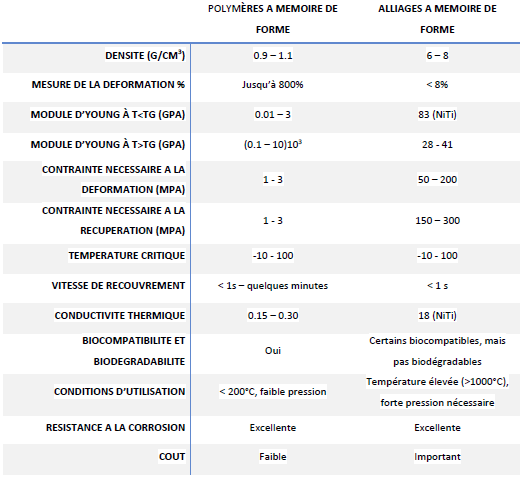
As described above, shape memory polymers have many advantages. However, they are not electrically conductive and have a much lower stiffness than shape memory alloys. In order to ensure their application in many fields, and to improve the above mentioned properties, it is necessary to design better performing materials: shape memory composites.
The shape memory composites are implemented thanks to two main families of fibers and particles:
– Conventional fibers and particles
– Multifunctional fibers and particles
A. Conventional fiber and particle shape memory composites
Conventional reinforcements such as carbon fiber, glass fiber, and Kevlar have been used to increase the mechanical strength of SMPs. These fillers can be designed in various forms, such as fabrics, mats or microfibers, and integrated into the SMP matrix to make it stiffer. Indeed, these fibers can support higher loads than the matrix alone, while maintaining the shape memory property provided by the SMP resin. Therefore, these materials have potential applications in self-deploying structures and vibration control structures.
Conventionally used fibers have several advantages and disadvantages:
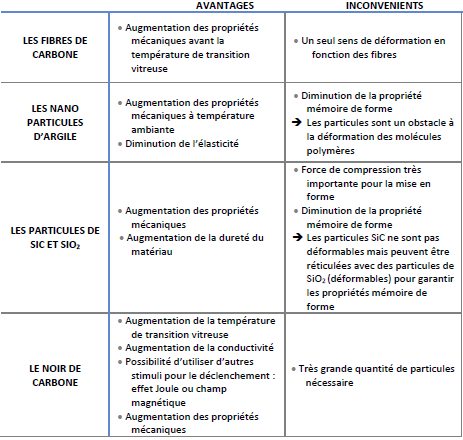
Despite the advantages of conventional fibers, it is necessary to pay special attention to multifunctional polymer composites with special fillers, which are able to keep the shape memory behavior intact, and at the same time exhibit higher modulus and strength.
B. Multifunctional fiber and particle shape memory composites
To fully utilize the shape-change capability of polymers, it is possible to incorporate reinforcements that perform more than one function. Recent studies have focused on reinforcing shape memory polymers with unconventional fillers such as shape memory alloys and carbon nanotubes. The use of these multifunctional fillers instead of conventional fillers helps to develop stronger, thermally stable and electrically conductive shape memory polymer composites.
The integration of shape memory alloys in the form of particles, short fibers, or continuous fibers into the matrix results in a multifunctional composite material that includes smart and self-deploying actuator applications. In general, SMP composites containing particles and short fibers perform a specific function, such as increasing electrical conductivity, improving magnetic response, and increasing matrix stiffness. While long and continuous fibers could be used as reinforcements to improve the mechanical properties and strength of the material.
A second route to obtain a multifunctional composite material with high stiffness, light weight, and high structural damping is to reinforce the polymer matrix with carbon nanotubes. CNTs have excellent mechanical, electrical, and magnetic properties, as well as a nanoscale diameter that make them an ideal reinforcing agent for high-strength polymer composites. Unlike carbon black, the addition of small amounts of CNTs also ensures high thermal stability, significantly increasing the glass transition temperature.
A. In the medical sector: the meatus plug
In order to treat dry eyes, the ophthalmologist seals the tear ducts by placing a meatus plug in the lacrimal meatus. This prevents the lacrimal fluid from flowing out through the tear duct. PolymerExpert has used its shape memory polymer technology to make an umbrella-shaped plug with a diameter of less than 0.1 mm that opens to close the canal thanks to the effect of temperature.
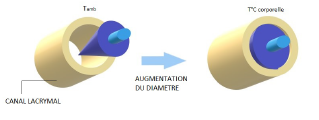
B. In the industrial sector: replacing a threaded rod
In the textile industry, operators used a threaded rod with a bolt system to place all the threads before launching the weaving machine. To increase productivity, PolymerExpert has developed shape memory rods. Thus, the bolts are easily threaded on the small diameter rod. When heated, the diameter of the rod increases and locks the bolts.
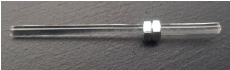
C. In the aerospace sector: deployable arms
In order to save mass, deployment devices (for solar panels for example) have been replaced by shape memory composites. These thermally and electrically conductive materials have the property to deploy simply thanks to an electric current brought by a battery or a resistor. The advantage of this technology is that it avoids the need for a heavy engine on a nano-satellite, coupled with articulated metal arms.
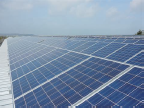