The first work carried out in this field is the work of Chamley who, as early as 1960, used the possibility of obtaining the controlled hardening of a mixture [methyl methacrylate (MMA)]/[poly(methyl methacrylate) (PMMA)], at a temperature much lower than that generally required by this type of polymerisation. The polymerisation of MMA, responsible for hardening, is the result of the combination of 2 complementary phenomenon: acceleration of the initiator decomposition and the gel effect.
Basic mechanism of cement mass setting
The accelerating decomposition of the initiator is achieved by oxidoreduction, a reaction with a low energy activation. In acrylic cements, the oxidation-reduction couple consists of the mixture benzoyl peroxide (BPO)/dimethyl-p-toluidine (DMPT) :
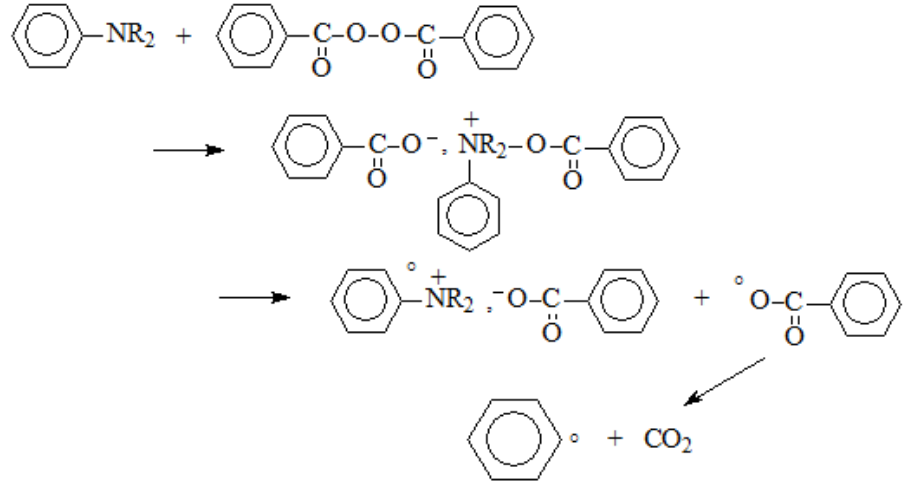
At a given temperature, the decomposition rate of BPO is controlled by the proportion of DMPT.
The gel effect (or Tromsdorff effect) is a phenomenon related to the difficulty of the active chains carrying a free radical to move in the highly viscous medium resulting from the dissolution of PMMA in MMA. The termination reactions that can only result from the meeting of 2 free radicals are then slowed down and polymerization accelerates because the system leaves the quasi-stationary state. In other words, the strong slowing down of the termination reactions induces an increase in the number of active chains and in the kinetic of polymerisation which can reach the explosive stage.
The cement formulation must take this phenomenon into account and also take into account the [BPO]/[MMA] and [BPO]/[DMPT] ratios so that the curing process of the mixture is completed in a time compatible with the surgical constraints (up to 24 hours).
The implementation of the process consists of mixing – just before the surgical act – on the one hand, PMMA, benzoyl peroxide, opacifying filler and possible solid additives with, on the other hand, MMA and DMPT. Polymerisation starts immediately at room temperature and continues until the system has fully set and the prosthesis is sealed.
Application of acrylic bone cement in arthroplasty
For most uses, cement acts by filling the crevices between the prosthesis and the bone, so there is no need for reciprocal adhesion. If necessary, however, this adhesion can be achieved by replacing part of the MMA with hydroxyethyl methacrylate (HEMA).
The initial viscosity of the mixture must be adapted to the type of use of the cement: very fluid for vertebroplasty, highly viscous for anchoring a femoral prosthesis, and of intermediate viscosity for anchoring a knee prosthesis.
In order to reduce the risk of infection during surgery, the cements are supplemented with antibiotics such as Gentamicin. The addition of a neutral filler, such as barium sulphate, acts as a radio-opacifier and allows radiographic monitoring of the seal.
The rise in temperature due to mass polymerisation causes necrosis of the tissues in contact with the cement. Attempts have been made to reduce the mass enthalpy of polymerization; the replacement of part of the MMA by heavy alkyl methacrylates has proved effective. However, in use, it was found that the increase in temperature – which appeared to be a disadvantage – helped the cauterisation of the blood vessels and was essential for the smooth running of the operation.