The design of materials capable of repairing themselves, either spontaneously or under the effect of a stimulus, makes it possible to improve their lifespan and their reliability while reducing maintenance costs. This approach, which is eco-responsible, reduces the consumption of polymer materials and the production of waste. This technology can be applied in many fields to restore the original appearance and properties of materials. PolymerExpert designs custom-made healing materials to best suit your needs.
Polymeric materials are passive structures consisting of irreversible covalent bonds. During their solicitation, the rupture of a certain number of bonds can lead to the formation of micro-cracks, which leads to a reduction in the properties of the material. The propagation of micro-cracks affects the integrity of the polymer structure (reduced service life, compromised safety) and can lead to material failure. An ideal polymer would be able to react to damage throughout its lifetime without changing the initial properties of the material. Take for example a telephone screen that repairs itself. The material becomes more reliable, its life span is increased while maintenance costs are reduced.
There are two different healing technologies:
– assisted healing, using healing agents (consumables),
– Self-healing (or self-healing).
Assisted wound healing is based on the release of monomers and catalysts stored within reservoirs dispersed in the polymer matrix. These reservoirs are usually capsules or vascularized networks. Upon damage, the rupture of the reservoirs allows the release of healing monomers that fill the crack by capillarity and polymerize, thus repairing the structure and preventing the growth of the crack.
The most widely used method to date is the dispersion of monomer capsules, such as dicyclopentadiene (DCPD), which will react by Ring Opening Metathesis Polymerization (ROMP) in the presence of Grubbs catalyst.
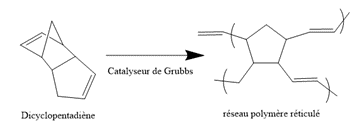
The advantage of this healing technique is that it is applicable to thermosets, which are widely used for structural applications. The cross-linked molecular structure gives these materials rigidity and stability. Therefore, they do not possess the chain mobility that is widely used for the self-repair of thermoplastics. Assisted healing allows for the repair of extensive damage, up to several cubic millimeters in size.

a) formation of the crack in the matrix, b) rupture of the capsules by crack propagation leading to the release of healing agents into the crack by capillary action, c) polymerization of the healing agents in the crack when they come in contact with the catalyst
However, the repair can only be carried out a limited number of times, as the healing agents are consumed. The manufacturing process is complicated by the addition of a monomer encapsulation step and the dispersion of the capsules within the polymer matrix.
Thermoplastic additives can also be used as healing agents in rigid matrices. An increase in temperature will cause the thermoplastic to flow in a molten state into the damaged areas. As the temperature decreases, the thermoplastic hardens, repairing the composite. This method is typically used to repair epoxy/fiberglass matrices.
Self-healing is an inherent healing ability of the material, which can heal an infinite number of times.
Self-healing technology relies on reversible bonds in the coating or material, does not affect the application procedure and is suitable for a wide range of polymers. In contrast to assisted repair, intrinsic self-healing is provided by reversible bonds that create a dynamic network opening and reform infinitely, with or without external stimuli. When self-healing is not activated by a stimulus, it is important that the polymer has high chain mobility.
The three main self-healing techniques used are reversible reactions creating dynamic covalent bonds, weak bonds (supramolecular polymers) or molecular entanglements.
The most commonly used reversible covalent bonds are the Diels – Alder reactions and disulfide bridges. The temperature of the thermal stimuli required to repair materials depends on the strength of the bond. Covalent bonds have a high binding energy (200-400 kJ/mol), the temperature required to open and close the temporary network is large (100-150°C).
Weak bonds, such as hydrogen bonds or π-stacks, allow repair at room temperature, without external stimulus. Polyurethane coatings, possessing many hydrogen bonds, are used in particular in the automotive industry, where the paint guarantees both the decorative appearance and the protection of the bodywork. These self-repairing paints reduce surface scratches within a few days at room temperature.
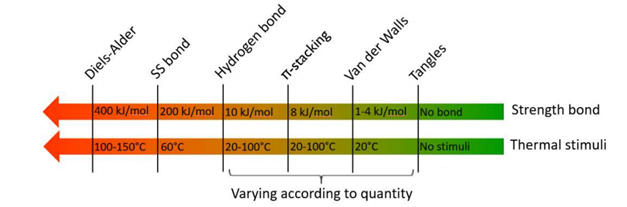
Another route to healing is structural self-repair, which is related to the ability of polymer chains to physically rearrange themselves in the material. Chain creep, or molecular interdiffusion, is applicable to thermoplastics.
In a polymer material, chain entanglements prevent lateral diffusion of the chains, which then diffuse by creep. The material then behaves like a solid at short times but heals at longer times. Healing takes place on freshly damaged surfaces, by re-contacting at a temperature above the glass transition. Progressively, the polymer chains enter into creep, the mechanical properties at the polymer-polymer interface increase while the crack repairs itself thanks to molecular diffusion at the interface. Increasing the temperature above the glass transition temperature, as well as increasing the healing time, improves the quality of the healing. This model of repair is used in particular in the field of paints.
Wool and O’Connor[2] suggested five model steps to explain the healing process by molecular interdiffusion:
- Rearrangement and approach of surfaces (1 and 2),
- Wetting of surfaces (3),
- Weak diffusion between surfaces (4)
- And diffusion, equilibrium and random distribution of chains (5).
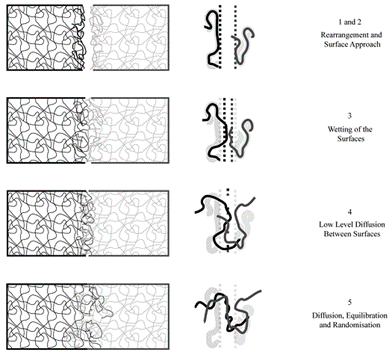
by molecular inter-diffusion
Self-healing makes it possible to repair cracks smaller than a cubic millimeter, theoretically infinitely.
Self-repairing polymers have their place in surface coatings. They allow for example to restore the appearance of the coating after a scratch. This property can be useful in cosmetics, with self-repairing nail polish for example, or in the automotive industry for car paints. They can also be used to guarantee the longevity of performance, particularly with regard to insulation properties or protection against corrosion, useful in the field of electronics.
One of the many advantages of self-healing is to improve the life span of materials, which is an important criterion for parts that are difficult to access, such as in satellites or in the medical field, especially with prostheses.
Self-healing floor coverings can also be interesting, with laminates that can be repaired with a hot mop. Bitumen capable of regenerating by melting thermoplastics has also been developed.
The luxury and technology sectors will also find interest in these materials, for example for watch or cell phone lenses.
1 White SR, Sottos NR, Geubelle PH, Moore JS, Kessler MR, Sriram SR, Brown EN, Viswanathan S. Autonomic healing of polymer composites, Nature 2001, 409:794-797. 2 Wool RP, O'Connor KM. A theory of crack healing in polymers. J. Appl. Phys. 1981;52:5953-5963.