The SAPHyR project (Photonic Hyperfrequency Aeronautical System in the Region) was born in 2017, carried by the ALPHA-RLH cluster and supported by the Regional Council of New Aquitaine and Occitania. For the companies selected for this project, the goal is to show their expertise through demonstrators at the Paris Air Show in June 2019.
This is a federating and structuring project for the regional territory. SAPHyR aims to create a global dynamic by developing synergies and complementarities by pooling resources and means.
PolymerExpert has therefore chosen to use its knowledge in the field of shape memory polymers and composites to propose a new object essential to the aeronautical sector : rivets.
Aeronautical structures are made up of an assembly of parts of considerable size. Moreover, these parts have more or less complex geometries and very varied properties. Most of them are assembled by rivets. The number of these rivets can be counted in millions for a structure such as an aircraft (1.6 million rivets on an A340). Rivet installation requires a large number of operations (drilling, deburring, chip removal, fixation removal), which are difficiently automatable because of the large number of tools. Rivets being made of metal alloys, represent a rather substantial mass.
To remove a conventional rivet it is necessary to break off the rivet head and tear off the body, which can weaken the peripheral structure. Sometimes it is even necessary to drill a larger hole in the structure in order to install a new rivet. A very wide range of rivet part numbers is required to cover the needs of the entire aircraft structure, depending on the diameter, length and composition of the rivets to be used.
Motivated by fuel economy, aircraft manufacturers are engaged in a technological race to minimize the weight of their aircraft. In order to reduce the total weight of an aircraft, PolymerExpert proposes to replace metal rivets on aircraft with shape memory composite rivets. Composite rivets should be an advantageous replacement for metal rivets, with an estimated weight saving of 50% and equivalent mechanical properties.
These shape memory rivets can be removed without imposing any stress on the structure. To do this, the rivets simply need to be ironed in their rubbery state and removed using a suitable tool. Thus, the range of rivets required for an aeronautical structure could be reduced thanks to their diameters adapting to the diameter of the hole during their deployment. They could also avoid problems of corrosion of structures due to their watertightness.
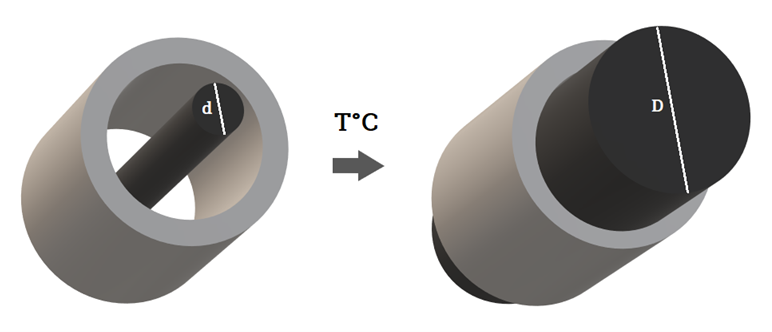
Figure 1: Schematic of rivet deployment under the action of heat
If you have any questions about this, please contact us !