Depuis les années 1950, l’encapsulation de molécules actives est devenue incontournable dans de nombreux domaines industriels. En effet, le confinement d’actifs offre plusieurs intérêts : la protection vis-à-vis de l’environnement extérieur, la manipulation plus sécure de produits dangereux, la libération contrôlée de molécules actives, le masquage de goûts, d’odeurs, de couleurs ou encore la manipulation de liquide sous forme de solide [1].
Mais alors qu’entend-t-on lorsque l’on parle d’encapsulation ?
Il s’agit de l’ensemble des technologies conduisant à des particules individualisées constituées d’un matériau enrobant et d’une matière active. En fonction de la taille des particules on parlera de microencapsulation (entre 1µm et 1mm), nanoencapsulation (10ène – 100ène de nm) ou minigranule (>1mm).
De nos jours, les matières actives sont d’origine très variées : principes actifs pharmaceutiques, ingrédients cosmétiques, additifs alimentaires, produits phytosanitaires, essences parfumées, micro-organismes, cellules vivantes, catalyseurs ou bien encore agents pour d’auto-réparation… [2-4].
PolymerExpert s’est spécialisé dans plusieurs méthodes d’encapsulation au travers de projets aux applications diverses et variées.
L’encapsulation conduit à des particules solides qui sont souvent de forme sphérique mais qui selon certains procédés peuvent aussi être de forme non régulière. Deux types de microstructures existent : les capsules ou les sphères.
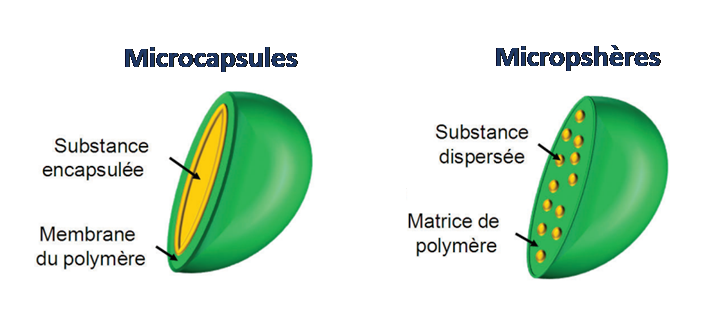
Les capsules : particules sphériques creuses, de type cœur-membrane, aussi appelé « core-shell » ou système réservoir. Le cœur est constitué de substance active, l’agent encapsulant formant l’enveloppe. Le taux d’encapsulation (teneur en matière encapsulée) peut être très élevé allant jusqu’à 85-90%g/g.
Les sphères, aussi appelé système matriciel : la particule est constituée d’une matrice polymère dans laquelle la substance active est dispersée à l’état moléculaire ou particulaire. Du fait de sa structure, le taux d’encapsulation reste relativement faible, de 20 à 30%g/g.
La substance à encapsuler peut être hydrophile ou lipophile, liquide ou solide et le procédé pour son encapsulation doit être choisi pour éviter toute dégradation de son activité. Par exemple, l’encapsulation de parfum sera préférentiellement réalisée par un procédé dit « froid » tel que le met en œuvre PolymerExpert avec son unité de photopolymérisation sous ultra-violet.
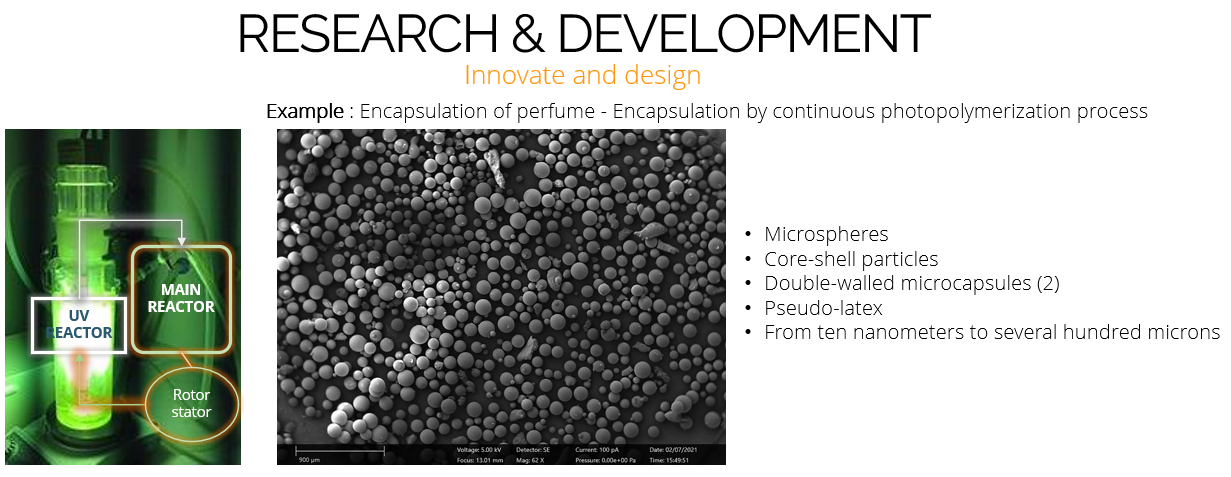
Les matériaux enrobants peuvent être des polymères d’origine naturelle (gélatine, chitosan, alginate de sodium, etc.), des polymères semi-synthétiques (dérivés cellulosiques), des polymères synthétiques (acryliques, styréniques, PEG, PPG, PLA…) ou bien encore des lipides solides (acides gras, cire de carnauba…).
Le choix de la matrice ou membrane doit être fait en fonction de l’application, pour garantir la stabilité des particules dans le produit fini (ex. stabilité hydrolytique dans les adoucissants) ou encore la facilité de libération de l’actif (ex. fragilité mécanique pour la cicatrisation de rayure). Différents autres facteurs physico-chimiques comme la charge électrique de surface, la mouillabilité, la porosité ou l’épaisseur orienteront le choix du polymère.
La nature de l’enrobant, au même titre que l’état physique de l’actif, impacte fortement la cinétique de libération.
Pourquoi encapsuler de la matière ? L’encapsulation est un moyen de programmer une activité chimique ou biologique, de la retarder ou de l’activer sur commande. En effet, la molécule active n’interagit avec le milieu extérieur que lorsque la barrière polymère est « levée ». Pour lever la protection de la membrane, ou matrice polymère, il existe différents mécanismes selon que l’on souhaite une libération instantanée (Figure 2) ou progressive (Figure 3).
Dans le premier cas, la totalité de l’actif contenu dans la particule est libérée rapidement, c’est une libération déclenchée.
La libération déclenchée : les capsules présentent une membrane étanche, qui se brise ou fond de façon brutale sous l’effet d’un stimuli extérieur (pression, fissure dans la matrice, pH, température etc.). C’est par exemple ce qui est attendu dans les systèmes d’autoréparation de peinture où la libération de la substance active permet d’apporter une réparation esthétique à une rayure mais aussi une protection contre la corrosion ultérieure du support.
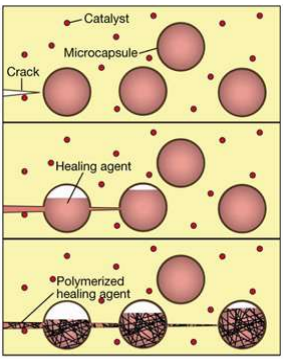
Dans le cas où la libération de l’actif doit être progressive, deux mécanismes principaux existent et décrivent l’action prolongée.
La libération prolongée : Ce type de libération a lieu aussi bien avec des sphères que des capsules. Deux mécanismes existent et cohabitent le plus souvent : la diffusion passive et la dissolution/dégradation de la paroi. Les cinétiques de libération obtenues sont différentes.
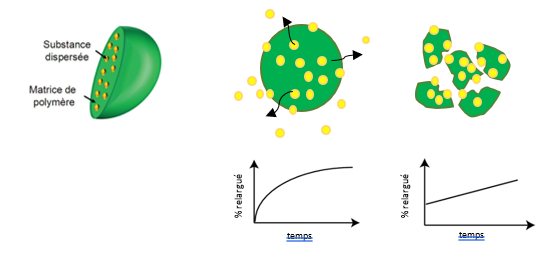
Ce mode d’action est notamment très recherché dans la pharmaceutique où l’activité contrôlée et prolongée du médicament est souhaitée. Des microsphères biodégradables permettent par exemple la délivrance retardée de médicaments, comme celle d’antidouleurs, qui ne seront activés que lors de l’hydrolyse acide dans l’estomac de la matrice polymère. De même, l’élaboration de nanoparticules biocompatibles, en polylactide biodégradables par exemple, permet la libération lente et ciblée de principe actif antitumoral.
Trois grandes classes de procédés peuvent être mis en place pour élaborer la plus performante des capsules :
- Les procédés physico-chimiques basés sur des variations de solubilité des agents enrobants
- Des procédés chimiques au cours desquels se déroulent simultanément la synthèse de la membrane/matrice et l’encapsulation de l’actif
- Les procédés mécaniques, comme l’extrusion ou l’enrobage
Le descriptif, non exhaustif, de certains d’entre eux est ici illustré par quelques images de nos réalisations.
Les Procédés physico-chimiques
- La coacervation
La coacervation décrit un phénomène de désolvatation de macromolécules, conduisant à une séparation de phase au sein d’une solution. Ce phénomène est déclenché par une modification du milieu (température, pH, addition de non-solvant, addition d’électrolyte ou d’un polymère incompatible). A l’issu de cette séparation, deux phases sont identifiables : le coacervat (riche en polymère et pauvre en solvant) et le surnageant (riche en solvant et pauvre en polymère). L’actif est encapsulé en le dispersant dans le milieu. Si les conditions sont favorables, le coacervat formé vient se déposer à la surface des gouttelettes (Figure 4).
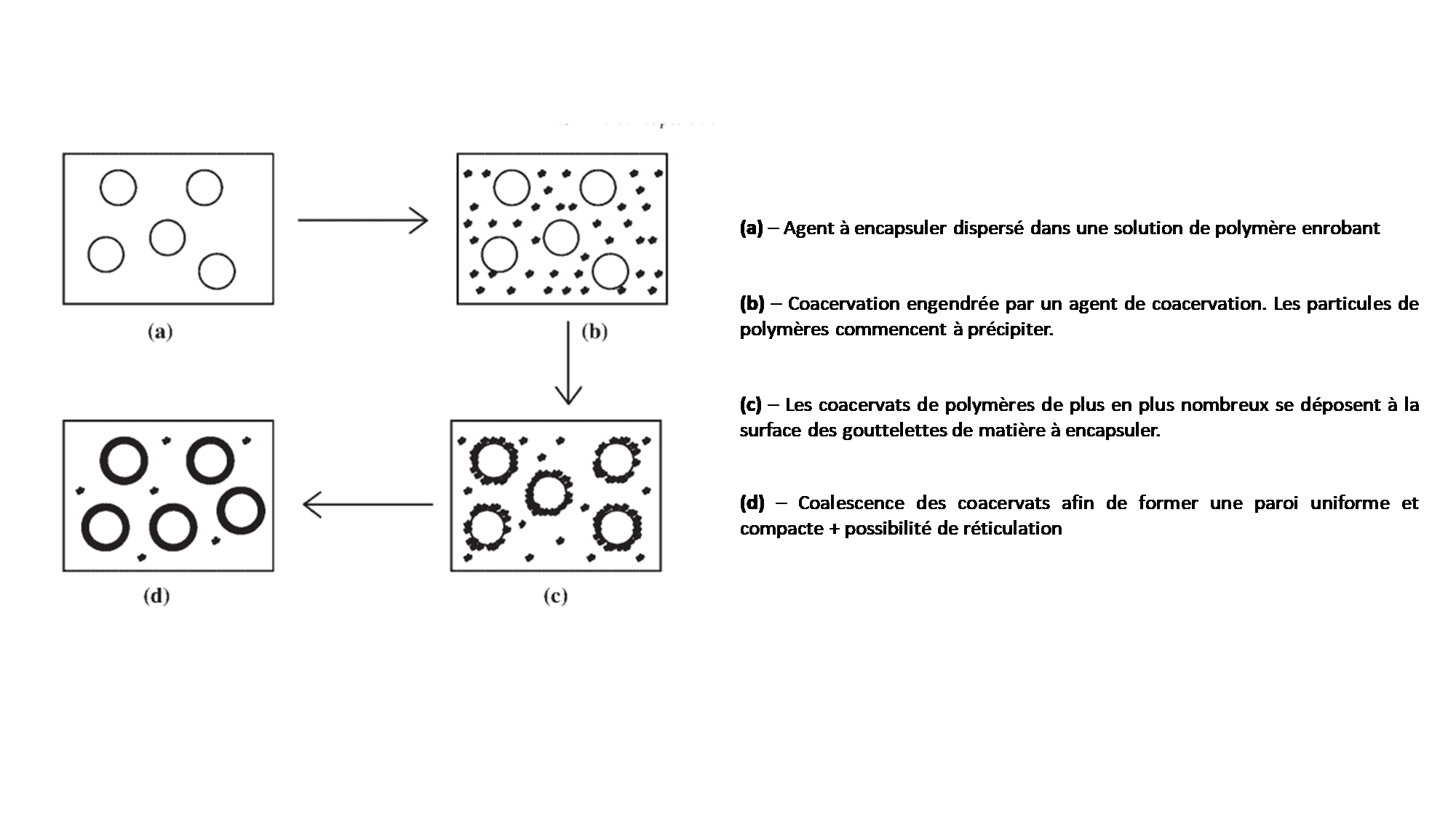
La coacervation simple n’implique qu’un seul polymère, pouvant être hydrosoluble ou organosoluble dans le processus d’encapsulation. Généralement, ce processus permet d’obtenir des microcapsules même s’il est possible d’obtenir des microsphères lorsque la proportion de substances à encapsuler est très faible par rapport au coacervat.
La coacervation complexe implique deux polymères : un polymère chargé négativement et un second chargé positivement. La désolvatation se fait par la neutralisation des charges engendrée le plus souvent par une variation de pH. Le matériau à encapsuler est, dans un premier temps, dispersé dans une solution aqueuse de polyélectrolyte chargé négativement puis une solution aqueuse contenant le second polymère (charge opposée) est introduite dans l’émulsion. Les polymères interagissent entre eux. Le coacervat vient se déposer sur la surface des gouttelettes lorsque les charges sont neutralisées par la variation du pH.
Ce procédé de microencapsulation est beaucoup utilisé dans les domaines de la pharmaceutique, de la médecine ou encore de l’alimentaire en raison notamment de la biodégradabilité des parois permettant un relargage prolongé et contrôlé. Parmi les agents enrobant plus répandus se trouvent les protéines animales avec notamment la gélatine, les protéines végétales comme la gliadine et les dérivés cellulosiques comme Hydroxypropyl Methylcellulose (HPMC) ou encore l’alginate.
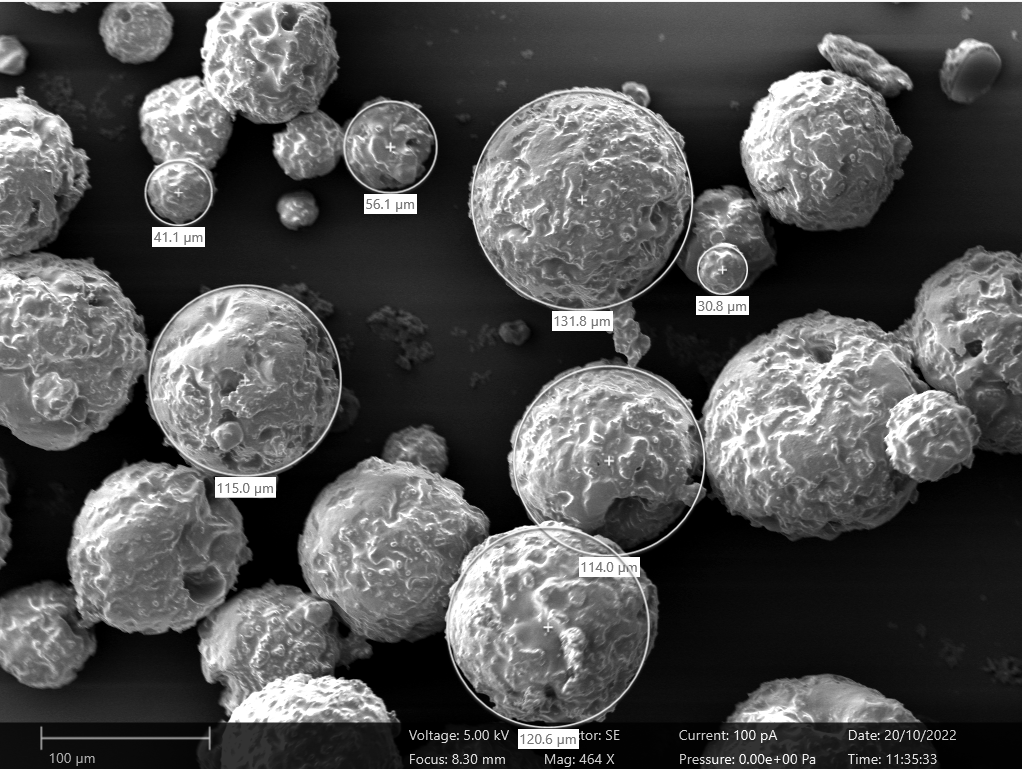
- Emulsification – évaporation de solvant
Ce principe repose sur l’évaporation de la phase interne d’une émulsion sous agitation (Figure 6). L’agent à encapsuler est, soit dissout, soit dispersé dans une phase organique constituée d’un polymère (agent enrobant généralement hydrophobe) solubilisé dans un solvant organique volatil (1). La solution organique (solvant + matière encapsulée + polymère) est émulsionnée sous agitation dans une phase dispersante aqueuse qui n’est pas un bon solvant du polymère. L’émulsion est stabilisée par ajout de tensio-actifs (2). Une fois l’émulsion stable, le solvant diffuse progressivement dans la phase dispersante sous agitation puis s’évapore (3). L’actif est enfin encapsulé soit par précipitation du polymère dans les gouttelettes formant des microsphères soit par migration des chaînes de polymère à l’interface des gouttelettes formant des particules « core-shell » (4).
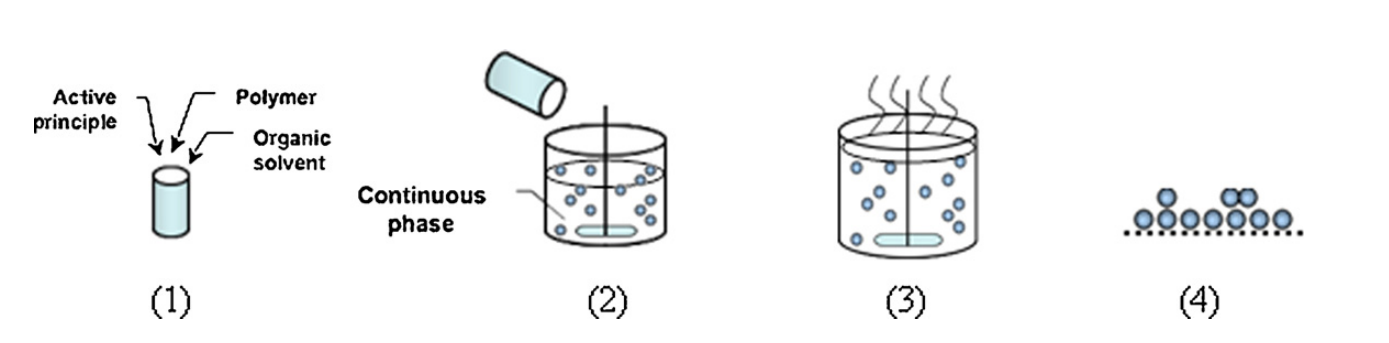
Les particules ainsi formées peuvent être collectées par centrifugation ou filtration. Des particules micrométriques thermoplastiques à propriétés particulières ont ainsi été élaborées par PolymerExpert pour l’élaboration de fluides amortisseurs pour des applications aérospatiales.
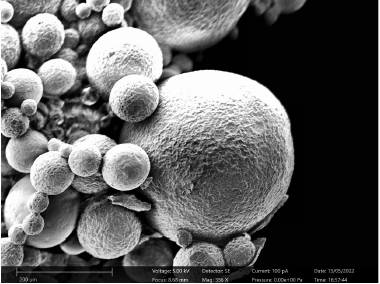
- La gélification thermique (Procédé « hot-melt »)
Ce procédé repose sur la fusion du matériau d’enrobage. La matière à encapsuler est, soit dispersée (si insoluble), soit dissoute dans ce matériau fondu. Le principe de cette technique est présenté en Figure 8. La phase continue (polymère + matière active) est émulsionnée dans une phase dispersante. Lors de la mise en émulsion, il est important que la température de la phase dispersante soit maintenue supérieure à la température de fusion du matériau d’enrobage. La solidification des particules a lieu par une refroidissement brutal du milieu en dessous de ladite température de fusion. La matière à encapsuler peut-être lipophile ou bien hydrosoluble.
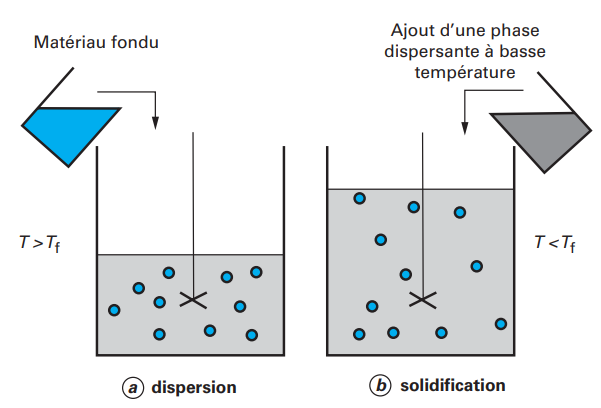
Ce procédé est utilisé par PolymerExpert pour des applications cosmétiques pour l’élaboration de particules souples, perles évanescentes, dans lesquelles des actifs solaires et parfumés sont encapsulés et suspendues dans une phase aqueuse à la texture crémeuse.
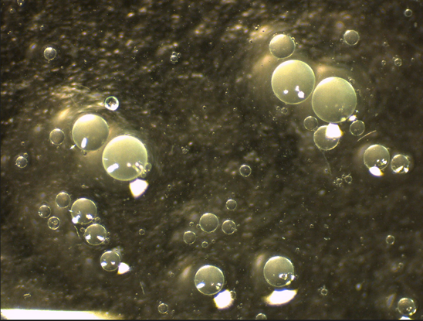
Procédés chimiques
Lors des procédés d’encapsulation chimiques, les agents polymériques enrobant ne sont pas formés au préalable. La polymérisation se fait donc dans le milieu réactionnel et les matières à encapsuler ne doivent donc pas réagir avec les monomères.
- La polycondensation in-situ
Dans ce procédé, le matériau à encapsuler est émulsionné dans une phase aqueuse contenant deux monomères réactifs A et B (hydrosolubles). Le principe est schématisé dans la Figure 10. Par augmentation de la température du milieu, les monomères copolymérisent par polycondensation, formant des oligomères partiellement solubles dans le milieu. Les agrégats de polymères, devenant de plus en plus insolubles dans le milieu se déposent à la surface des gouttelettes à encapsuler. Des capsules de type « core shell » sont alors obtenues par réticulation de la paroi solide.
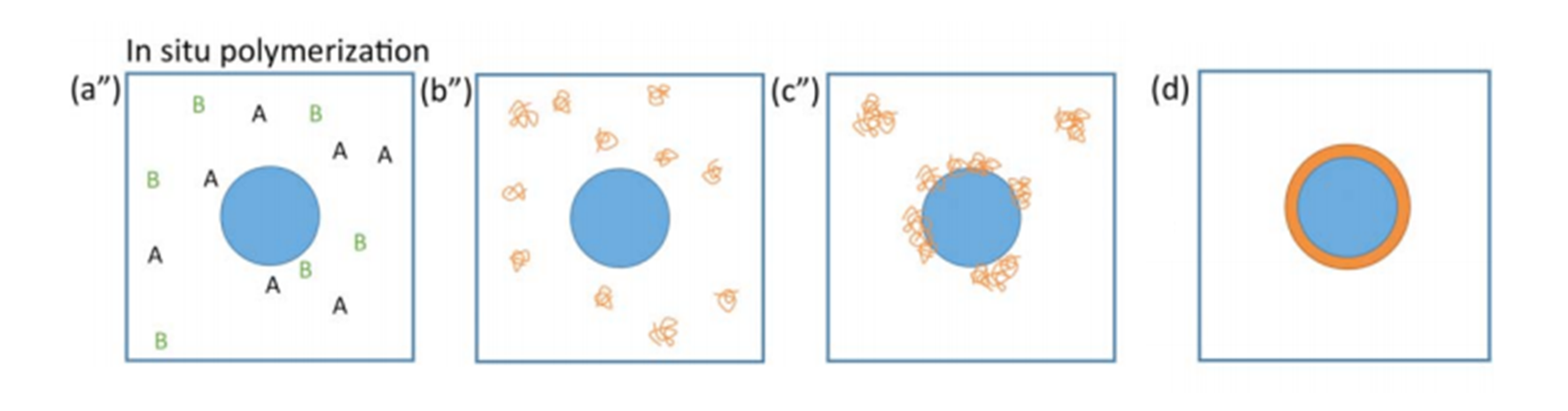
La quasi-totalité des microcapsules obtenues par polycondensation in-situ possède une paroi de type aminoplaste. Ces résines obtenues via la réaction de polycondensation entre l’urée, le formaldéhyde et des dérivés mélaminés ont permis à PolymerExpert d’élaborer des capsules actives pour l’autoréparation de charges propulsives.
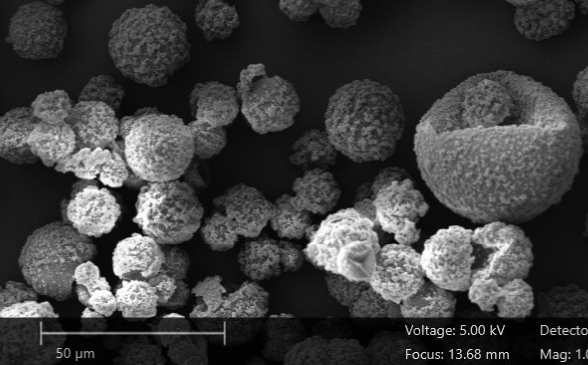
- La polymérisation radicalaire in-situ
Il est possible de distinguer 4 processus de polymérisation radicalaire in-situ : (i) l’émulsion, (ii) la mini-émulsion, (iii) la suspension et enfin (iv) la dispersion.
Dans le cadre de la polymérisation radicalaire in-situ via émulsion ou mini-émulsion, l’amorceur radicalaire est de type hydrosoluble et peut être décomposé par voie thermique ou UV. L’encapsulation et la polymérisation se font à l’intérieur de micelles. Les particules obtenues sont de l’ordre du µm pour l’émulsion et de la centaine de nm pour la mini-émulsion.
Lors de la polymérisation en suspension, l’amorceur radicalaire est organosoluble et se trouve dans les gouttelettes de monomères contenant l’agent à encapsuler. La polymérisation se fait donc dans les gouttelettes de monomères.
Dans le cadre de la polymérisation en dispersion, les monomères et la matière active sont initialement solubilisés dans la phase continue. Les oligomères en croissance, une fois qu’ils ont atteint une certaine longueur (critique), précipitent pour former des agrégats qui sont stabilisés par des tensio-actifs présents dans la phase continue. Ces agrégats constituent les nucléus, lieux de croissance des particules finales de polymère dont la taille varie entre 1-15 µm [6].
Grace à ce procédé PolymerExpert a conçues des particules à paroi acrylique pour l’autoréparation, mécaniquement très résistantes et pouvant être incorporées par malaxage pour la mise en œuvre de matériaux composites (Figure 12). Des images au microscope électronique à balayage révèlent une surface de sphère ressemblant à une « balle de golf », et un intérieur spongieux avec une matrice acrylique très aérée contenant l’actif.
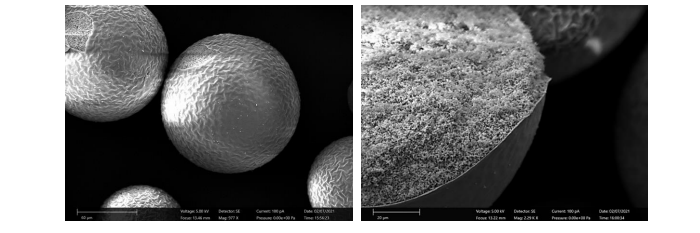
A toutes ces techniques chimiques et physico-chimiques d’encapsulation s’ajoutent les procédés mécaniques tels la nébulisation-atomisation (« spray-drying »), l’enrobage en lit fluidisé ou encore l’enrobage.
Procédés diverses, matériaux polymères nombreux, le choix est large pour masquer, protéger ou délivrer des principes actifs