Le passage de la synthèse d’un polymère de l’échelle du laboratoire au stade pilote et enfin à la production à grande échelle est un processus complexe et ardu qui nécessite des compétences et des technologies spécialisées. Tout d’abord, la conception d’un polymère à l’échelle du laboratoire est un processus très technique qui implique l’utilisation de diverses méthodes de synthèse et de diverses techniques d’analyse. Une fois que le polymère a été conçu et synthétisé à l’échelle du laboratoire, il est ensuite nécessaire d’effectuer des études de faisabilité et des tests sur le polymère à l’échelle pilote. Ces études sont nécessaires pour comprendre la faisabilité de la synthèse du polymère à des échelles plus grandes. Ils comprennent également des tests pour vérifier la qualité et la stabilité du polymère. Une fois que les études de faisabilité et les tests ont été effectués avec succès à l’échelle du laboratoire et du pilote, le polymère peut être synthétisé à grande échelle.
Le processus d’industrialisation d’un nouveau polymère nécessite l’intervention tout d’abord de plusieurs équipes avec des compétences et des savoir-faire différents.
L’équipe Recherche & Développement, avec les ingénieurs et techniciens ayant participé à la réussite du projet partage le dossier technique, incluant l’historique de conception et le cahier des charges. Ensemble, ils statuent sur les paramètres clés du produit et du process pour entrer dans la phase d’industrialisation. Ils font généralement le choix et la vérification des moyens de production et de contrôle.
L’équipe Marketing valide la faisabilité économique de l’industrialisation. En effet, avant de se lancer dans un tel processus, il est impératif de balayer l’ensemble des aspects économiques notamment par la réalisation d’une étude de marché.
L’équipe Hygiène, Sécurité et Environnement contribue à l’élaboration d’une analyse de risque sécurité. L’identification, l’analyse et le classement des risques permettront de définir les actions de prévention les plus appropriées, couvrant les dimensions techniques, humaines et organisationnelles. Une réunion se tient alors entre les chimistes et les personnes en charge de la sécurité des procédés pour se poser les bonnes questions : « Que se passerait-il si… ? » … si le système de refroidissement s’arrêtait, si le condenseur tombait en panne, si tout le réactif était ajouté trop rapidement ? etc. Toutes les phases de la synthèse sont ainsi analysées : la préparation du matériel, le chargement, la réaction chimique, le traitement des déchets, le stockage, pour faire en sorte que la probabilité d’un accident soit proche de zéro.
L’équipe Qualité garantit le respect des normes ISO 9001 et ISO13485. Elle apporte pour cela, ses compétences afin de réaliser une analyse de risque produit et process. En soutien, elle constitue un Master Batch Record, regroupant les documents nécessaires à la traçabilité et à la conformité du produit. Ce dossier complet est constitué des spécifications des matières premières, produit fini, et conditionnement. Il regroupe également les instructions de travail et le dossier de fabrication, communément appelé, le « Standard Operating Procedure » qui décrit toutes les étapes et les activités appropriées à la production. Le « Master Batch record » est aussi enrichi par les validations de méthode analytiques inhérentes au produit, aux études de stabilité du produit fini, jusqu’à la validation des étiquettes produit, matières premières, et contrôle en cours de process.
L’équipe de Production valide le choix des équipements et réfléchit à la conception de nouveaux équipements indispensables si les installations ne sont pas adaptées. Elle commence à travailler sur des unités de taille intermédiaire (échelle pilote, pré-séries) sur des quantités allant de quelques centaines de grammes à plusieurs dizaines de kilogrammes pour limiter les risques liés à la sécurité et/ou à des pertes financières en cas de non-conformité du produit. La taille des unités de fabrication augmente après validation d’un certain nombre de paramètres et l’assurance de la reproductibilité des produits obtenus ; l’objectif étant d’atteindre la taille de batch économiquement la plus favorable selon l’étude Marketing.
Le logigramme ci-dessous présente de manière schématique le processus régissant le passage du stade laboratoire au stade industriel. Il est extrait du manuel Qualité de PolymerExpert et fait référence à des documents internes à la société.
Capabilité procédé : Il s’agit de l’aptitude d’un procédé à produire de manière répétée et permanente un résultat conforme à des spécifications données. Elle traduit le niveau de risque qu’un procédé produise un résultat non conforme.
Cette capabilité se mesure par l’indice Cp :

Centrage : Spécificité d’un procédé à produire des résultats centrés vis-à-vis de spécifications établies. Le centrage se mesure par l’indice Cpk :

Paramètre clé ou critique : Tout paramètre dont une faible dérive peut générer des écarts importants au niveau du résultat final.
Production série : Production maîtrisée utilisant les ressources (humaines, documentaires et matérielles) du service production et permettant la réalisation d’un produit en quantités compatibles avec les besoins commerciaux.
Production présérie : Réalisée avec les ressources de production série mais sur une quantité faible pour limiter les risques liés à la sécurité et / ou les pertes financières en cas de produit non conforme. Une production présérie nécessite une surveillance accrue (contrôles qualités supplémentaires, surveillance physique permanente, …)
Production série surveillée : Production série nécessitant une surveillance accrue (contrôles qualités supplémentaires, surveillance physique permanente, …)
Validation technique : Preuve que le process permet d’obtenir un produit conforme. Cette validation passe par 3 productions.
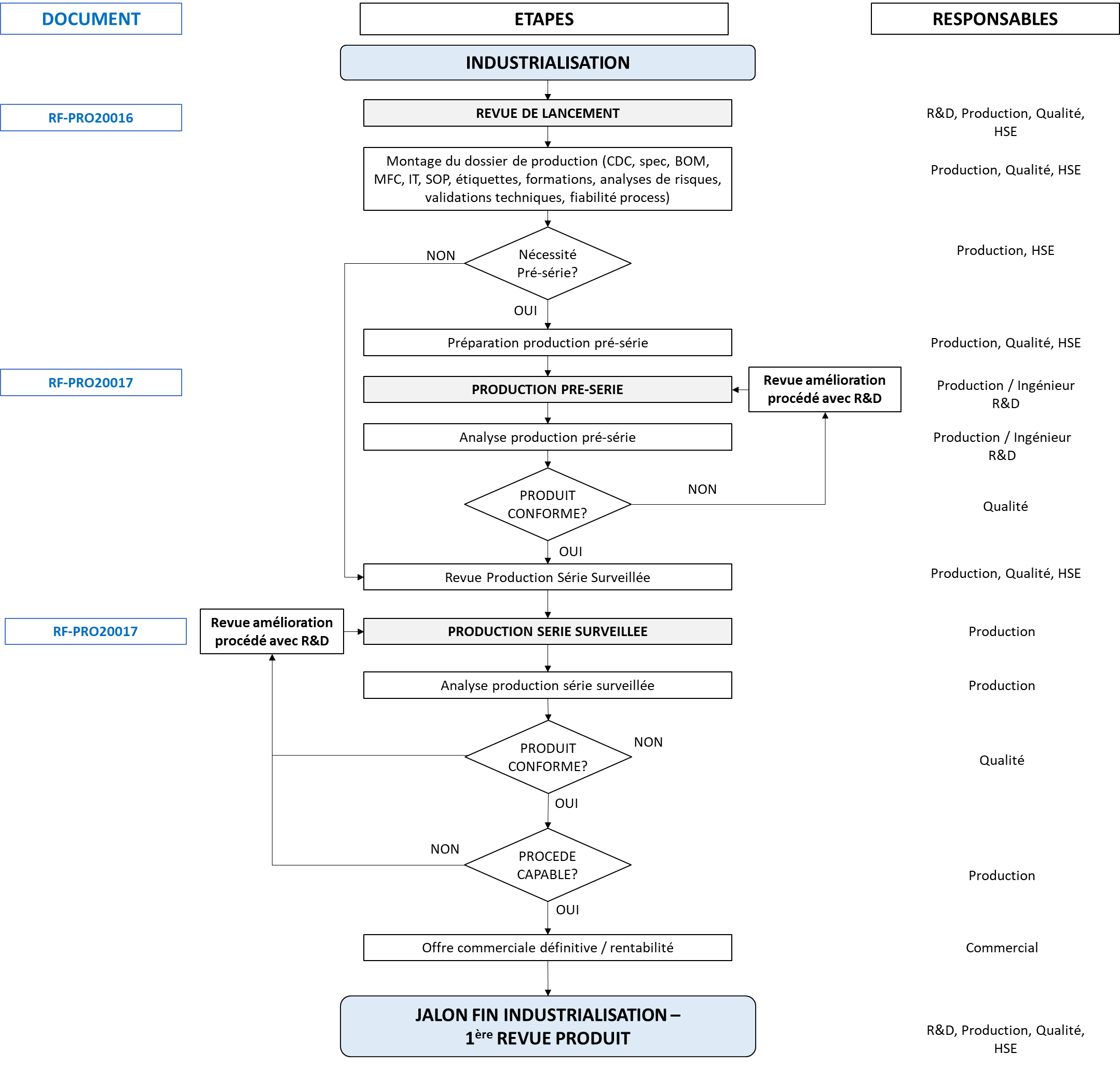
Chaque procédé d’industrialisation est différent ; le nombre de paramètres à fiabiliser dépend bien entendu de la complexité de la synthèses entreprise.
Dans le secteur de la chimie, passer du stade laboratoire au stade industriel est sans doute plus complexe que dans d’autres secteurs industriels. Les réactions chimiques sont dirigées par des centaines de paramètres qui ne sont pas forcément tous connus. Beaucoup de paramètres très importants sont pris en compte lors de la montée en échelle, comme la température, la pression, le temps d’introduction des réactifs, l’agitation…
L’objectif est d’optimiser la valeur de ces paramètres et de connaître l’impact de leur variation sur la qualité d’un produit et sur son rendement.
Cependant, deux paramètres que sont les transferts de chaleur et l’agitation doivent systématiquement être pris en compte.
L’une des difficultés rencontrées durant le scale-up est liée aux transferts de chaleur. Une montée en échelle en chimie signifie automatiquement l’utilisation d’un équipement de plus grosses capacités ce qui modifie de manière significative les échanges de chaleur.
Un autre paramètre important à considérer est l’agitation (le type d’agitation et la vitesse d’agitation notamment). On sait qu’augmenter la probabilité de rencontre de deux molécules de réactifs c’est augmenter la vitesse de la réaction ». Une agitation efficace améliore la cinétique de réaction et le transfert thermique. Un mauvais mélange peut engendrer des réactions secondaires, des dégradations et même pas de réaction du tout.
L’ajustement de ces paramètres nécessitent une certaine expertise accompagnée d’une grande expérience.
Confier votre projet d’innovation à PolymerExpert permet d’avoir recours à un prestataire spécialisé qui offre une solution clé en main. En effet, nous sommes à même de prendre en charge votre projet du TRL 1 au TRL 9, c’est-à-dire de l’idée à l’industrialisation.
Pour mener à bien le développement industriel d’un procédé de fabrication, les équipes de PolymerExpert s’appuient sur les compétences de docteurs et d’ingénieurs chimistes, d’analystes, d’experts en sécurité des procédés, et en développement technologique et sur celles des opérateurs.
PolymerExpert dispose de spécialistes en Recherche & Développement, analyses, marketing, réglementaire, qualité et transposition industrielle interagissant quotidiennement et intervenant très régulièrement tout le long du projet.
Au-delà d’une forte expertise, nos installations aussi bien nos réacteurs de synthèse de capacité allant de 1L à 800 L et nos équipements analytiques sont un véritable atout pour votre montée en échelle. Ces derniers rendent possibles des analyses déterminantes, des In process Control (IPC) ou encore des analyses sur le produit fini, permettant une efficacité et une rapidité et garantissant une reproductibilité des produits fabriqués.
Notre approche selon les standards ISO 9001 et ISO 13485 est un gage de rigueur et de traçabilité des projets entrepris.
Notre notation EcoVadis Platinium est une preuve de notre engagement environnemental, sociétal et éthiques ; des ingrédients indispensables au succès d’un nouveau produit sur le marché.
Ce choix de mode opératoire permet à PolymerExpert de réaliser une production technique et économiquement viable tout en répondant aux exigences qualités et aux contraintes réglementaires.
Nous produisons actuellement plus d’une dizaine de polymères différents pour notamment les secteurs des dispositifs médicaux et la cosmétique.