Il est d’usage de distinguer quatre grandes classes de matériaux :
– les métaux et leurs alliages ;
– les céramiques et les verres ;
– les polymères ;
– les matériaux composites.
Parmi ces classes, trois d’entre elles peuvent présenter une fonction mémoire de forme : les alliages, les polymères et les matériaux composites.
Les alliages à mémoire de forme, très largement utilisés au quotidien, font l’objet d’études depuis plus longtemps que les polymères à mémoire de forme. Ces deux groupes de matériaux intelligents ont des propriétés physiques, mécaniques, thermiques et électriques très différentes. Le mécanisme à l’origine de l’effet de mémoire de forme des AMF, provient des phases cristallographiques, appelées par analogie aux aciers, phase martensitique et phase austénitique. Le passage d’une phase à une autre se fait, soit par changement de température, soit par application d’une contrainte.
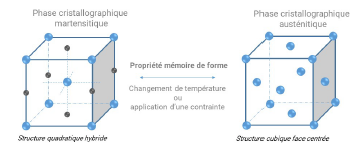
La transformation de phase des AMF présente plusieurs intérêts :
– Faible déplacement d’atomes (la composition chimique reste inchangée même localement) ;
– Iso volume ;
– Réversible.
Les alliages possédant des propriétés de mémoire de formes sont : certains laitons, certains alliages cuivre-aluminium et le nickel-titane, communément appelé nitinol. Ils sont utilisés, notamment, en orthodontie pour le redressement dentaire. Leurs caractéristiques mécaniques étant suffisamment importantes pour assurer l’arrangement des dents.
Les polymères, appelés communément “matières plastiques” se sont imposées dans tous les domaines. Utilisés des objets les plus communs jusque dans des applications les plus sophistiquées, leurs propriétés dépendent l’arrangement des chaines moléculaires les constituant. On distingue :
– les thermoplastiques ;
– les élastomères ;
– les thermodurcissables.
- Les polymères thermoplastiques sont « recyclables ». Ils sont constitués de macromolécules linéaires ou ramifiées. La cohésion entre les chaînes moléculaires est assurée par des liaisons de faible énergie de Van der Waals. Certains de ces polymères sont semi cristallins, ils contiennent alors des zones amorphes et des régions cristallines ordonnées.
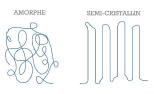
- Les élastomères sont des matériaux amorphes. Ils sont constitués de macromolécules linéaires reliées entre elles par quelques pontages entre leurs chaînes. La réaction chimique conduisant à ces liaisons entre chaînes s’appelle la vulcanisation et permet une réticulation du matériau.
- Les polymères thermodurcissables sont amorphes et sont formés par un réseau tridimensionnel de macromolécules. Ils sont réticulés, le taux de réticulation étant 10 à 100 fois plus élevé que dans les élastomères.
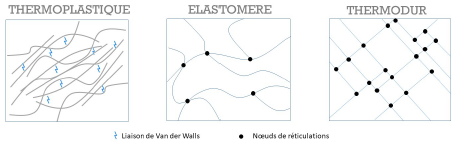
Lors d’un changement de température, un polymère peut traverser quatre domaines d’état structural délimités par trois températures spécifiques :
– la température de transition vitreuse Tg, cette transition étant observée dans la phase amorphe du polymère,
– la température de fusion Tf qui ne concerne que la phase cristalline du polymère si elle existe,
– la température de décomposition thermique Td où le polymère perd son intégrité.
Les propriétés mécaniques des polymères varient en fonction de leurs températures, ce qui leurs confèrent une “mémoire de forme”.
L’effet mémoire de forme est la capacité pour un matériau d’être déformé de manière stable dans un certain domaine de température et de retrouver sa forme initiale sous l’action d’un stimulus extérieur. Plusieurs stimulus peuvent être utilisés pour activer la mémoire de forme d’un polymère : l’eau, la chaleur, les ultraviolets, l’électricité, etc.
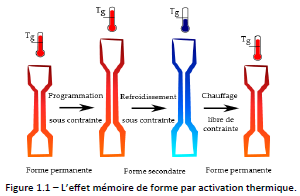
La figure 1.1 montre l’effet mémoire de forme d’un polymère répondant à un stimulus thermique : l’activation la plus utilisée à ce jour.
La première étape est la “programmation” du matériau : elle consiste à le déformer mécaniquement à chaud (T > Tg) jusqu’à obtenir la forme secondaire souhaitée. Durant la seconde étape, le matériau est refroidi, tout en maintenant la force appliquée. Puis, les contraintes sont relâchées, donnant lieu à un faible retour élastique du matériau. À ce stade, si aucun traitement thermique n’est appliqué, la forme secondaire est conservée. Finalement, la forme initiale, ou permanente, est restituée en chauffant le matériau libre d’efforts extérieurs. La température, au-delà de laquelle le matériau doit être chauffé pour fixer la forme secondaire et retrouver la forme permanente, est comprise dans le domaine de transition vitreuse du matériau (T>Tg).
L’effet mémoire de forme est plus ou moins intéressant selon la classe des polymères étudiés. Ils ont été classifiés, en se focalisant sur les liaisons chimiques entre les molécules, pour obtenir 4 catégories :
- 1. Le réseau thermodurcissable, vitreux, réticulé de manière covalente
Cette classe de polymères présente une large plage de température de transition vitreuse ajustable en fonction du monomère constituant la chaîne polymère. Il est possible de changer les propriétés mécaniques de ces polymères, en modifiant l’étendue de la réticulation et la température de transition vitreuse. Celle-ci joue donc un rôle important dans la détermination de leur application finale. Bien qu’ils aient une excellente capacité de récupération de forme, ces polymères, une fois traités, sont difficiles à remodeler. Cependant, en raison de leur large gamme de Tg et de leur module ajustable, ces polymères présentent des avantages par rapport aux autres classes décrites ci-dessous.
L’effet mémoire de forme spécifique aux polymères thermodurcissables
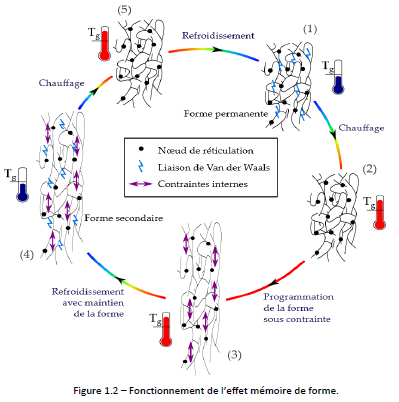
La figure 1.2 explique le fonctionnement de la mémoire de forme d’un polymère thermodurcissable. Dans sa forme permanente à température ambiante en phase (1), la rigidité du polymère est assurée par les liaisons de Van der Waals. En chauffant (2), ces liaisons disparaissent et permettent la mobilité des chaînes dans la limite des noeuds de réticulation (l’allongement du matériau sera d’autant plus élevé que la longueur des chaînes entre noeuds de réticulation est grande). Le polymère peut donc être déformé (3). Des contraintes internes apparaissent car la conformation des molécules ne correspond plus à leur état stable. En maintenant la déformation et en refroidissant (4), les liaisons de Van der Waals se reforment et maintiennent le polymère dans la forme secondaire. Par chauffage, les liaisons de Van der Waals se rompent, et le polymère reprend sa forme permanente sous l’effet des contraintes internes.
Cette mémoire de forme des polymères est connue depuis plusieurs décennies mais suscite ces dernières années, un regain d’intérêt dans le monde de la recherche, tout comme dans les milieux industriels, car de nombreuses applications innovantes sont envisageables. (Cf. V. Les applications des polymères à mémoire de forme).
- 2. Le réseau semi-cristallin, réticulé de manière covalente
Dans cette classe de SMP, en plus de la température de transition vitreuse (Tg), la température de fusion (Tm) des réseaux semi-cristallins peut également être utilisée pour déclencher un comportement de récupération de forme. Ces polymères sont faciles à travailler en dessous de leur température critique (Tg et Tm). Les vitesses de récupération de forme sont plus rapides que celles observées dans les matériaux thermodurcissables vitreux. Cependant, à l’instar des polymères vitreux thermodurcis, ils sont difficiles à remodeler une fois transformés. En outre, leur rigidité dépend du degré de cristallinité et donc indirectement de l’ampleur de la réticulation. Cela donne la possibilité d’avoir un module flexible et une récupération de forme rapide. Cette classe de matériaux comprend ; les caoutchoucs semi-cristallins et les élastomères à cristaux liquides. Bien qu’ils aient des taux de récupération de forme plus rapides, ils manquent de stabilité thermique. - 3. Le copolymère vitreux, réticulé physiquement
Il a été mis au point des méthodes spéciales pour la fabrication de polymères appartenant à cette catégorie de copolymères vitreux physiquement réticulés. Dans ce groupe SMP, les fractions molles et dures des thermoplastiques forment des liaisons transversales physiques qui donnent la super élasticité, ainsi qu’une Tg, qui favorisent le comportement de la mémoire de forme. La caractéristique des matériaux de cette classe est que, lorsqu’ils sont soumis à une température supérieure à la transition vitreuse (Tg) et à la température de fusion (Tm), le polymère coule et peut être traité pour obtenir une nouvelle forme. Cette capacité de traitement est possible car ils ne sont que physiquement réticulés, et possèdent une rigidité semblable aux thermodurcissables vitreux réticulés. - 4. Le copolymère à bloc semi cristallin, réticulé physiquement
La caractéristique de cette classe de polymères implique l’utilisation de la température de fusion (Tm) des copolymères séquencés pour déclencher la récupération de la forme. Pour ces polymères, le domaine mou cristallise. Ainsi, au lieu de leur Tg, la Tm pourrait être utilisée pour activer le polymère et la forme temporaire est ainsi fixée lorsque les segments mous cristallisent. Ce matériau peut être traité au-dessus de sa température de fusion et ses propriétés caoutchouteuses pourraient être ajustées en faisant varier le rapport segment souple / segment dur. En outre, la température de transition peut être contrôlée en modifiant les segments souples. Enfin, ces polymères peuvent être biodégradables et biocompatibles.
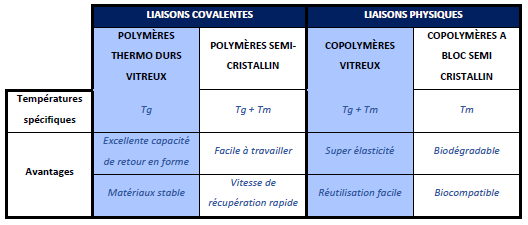
Les matériaux présentant les propriétés les plus intéressantes sont les polymères thermo durs. PolymerExpert travaille de façon plus spécifique sur ce type de matériaux mais peut également développer des SMP avec d’autres propriétés.
Si l’on compare, les alliages et les polymères à mémoire de forme, ces derniers présentent une déformation élastique élevée (environ 200%), une contrainte récupérable significative, un faible coût, une faible densité, une facilité de traitement, une large gamme de propriétés ajustables telles que la rigidité et la température de transition. Bien que les SMP présentent de nombreux avantages, la différence de module est notable lorsque l’on compare avec les SMA. Par ailleurs, ce module diminue lorsque le polymère passe en phase caoutchouteuse (domaine mou). Ils sont également incapables de transformation réversible sous forme d’alliages à mémoire de forme. Une comparaison de leurs propriétés est présentée dans le tableau ci-dessous.
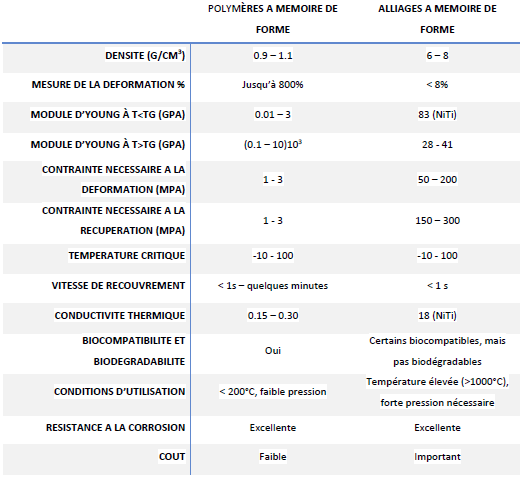
Comme décrit ci-dessus, les polymères à mémoire de forme présentent de nombreux avantages. Cependant, ils ne sont pas conducteurs électriquement et possèdent une rigidité très inférieure aux alliages à mémoire de forme. Afin de garantir leurs applications dans de nombreux domaines, et d’améliorer les propriétés susmentionnées, il est nécessaire de concevoir des matériaux plus performants : les composites à mémoire de forme.
Les composites à mémoire de forme sont mis en œuvre grâce à deux grandes familles de fibres et particules :
– Les fibres et particules conventionnelles
– Les fibres et particules multifonctionnelles
A. Les composites à mémoire de forme à fibres et particules conventionnelles
Des renforts classiques tels que la fibre de carbone, la fibre de verre et le Kevlar ont été utilisés pour augmenter la résistance mécanique des SMP. Ces charges peuvent être conçues sous différentes formes, telles que des tissus, des nattes ou des microfibres, et intégrées dans la matrice SMP pour la rendre plus rigide. En effet, ces fibres peuvent supporter des charges plus importantes que la matrice seule, tout en conservant la propriété mémoire de forme prodiguée par la résine SMP. C’est pourquoi, ces matériaux ont des applications potentielles dans les structures auto-déployables et les structures de contrôle des vibrations.
Les fibres utilisées de façon conventionnelle présentent plusieurs avantages et inconvénients :
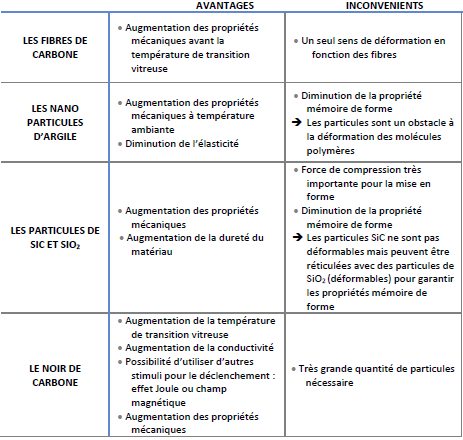
Malgré les avantages des fibres conventionnelles, il est nécessaire d’apporter une attention particulière aux composites polymères multifonctionnels dotés de charges spéciales, capables de conserver le comportement de mémoire de forme intact, et de présenter en même temps un module et une résistance plus élevés.
B. Les composites à mémoire de forme à fibres et particules multifonctionnelles
Pour utiliser pleinement la capacité des polymères à changer de forme, il est possible d’intégrer des renforts qui remplissent plus d’une fonction. Des études récentes ont porté sur le renforcement de polymères à mémoire de forme avec des charges non conventionnelles telles que des alliages à mémoire de forme et des nanotubes de carbone. L’utilisation de ces charges multifonctionnelles au lieu des charges classiques aide à développer des composites polymères à mémoire de forme plus solides, thermiquement stables et électriquement conducteurs.
L’intégration d’alliages à mémoire de forme sous forme de particules, de fibres courtes ou continues dans la matrice, permet d’obtenir un matériau composite multifonctionnel comprenant des applications d’actionneurs intelligents et auto-déployables. En général, les composites SMP contenant des particules et des fibres courtes remplissent une fonction spécifique, comme augmenter la conductivité électrique, améliorer la réponse magnétique et augmenter la rigidité de la matrice. Alors que les fibres longues et continues pourraient être utilisées comme renforts pour améliorer les propriétés mécaniques et la résistance du matériau.
Une seconde voie pour obtenir un matériau composite multifonctionnel, léger, avec une grande rigidité, et un amortissement structural important, est de renforcer la matrice polymère à l’aide de nanotubes de carbone. Les NTC présentent d’excellentes propriétés mécaniques, électriques et magnétiques, ainsi qu’un diamètre d’échelle nanométrique qui en font un agent de renforcement idéal pour les composites polymères haute résistance. Contrairement au noir de carbone, l’ajout en faible quantité de NTC permet également de garantir une grande stabilité thermique, en augmentant de façon significative la température de transition vitreuse.
A. Dans le secteur médical : le bouchon méatique
Pour le traitement de la sécheresse oculaire, l’ophtalmologiste procède à l’obturation des canaux lacrymaux par la pose d’un bouchon méatique dans le méat lacrymal. Ainsi le liquide lacrymal n’est plus évacué par le biais de ce canal. PolymerExpert a utilisé sa technologie de polymère à mémoire de forme pour faire un bouchon en forme de parapluie d’un diamètre inférieur à 0.1 mm qui vient s’ouvrir pour obturer le canal grâce à l’effet de la température.
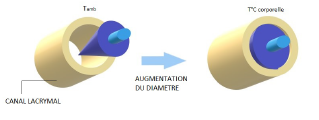
B. Dans le secteur industriel : le remplacement d’une tige filetée
Dans l’industrie textile, les opérateurs utilisaient une tige filetée avec un système de boulonnerie pour placer tous les fils avant lancement de la machine de tissage. Pour gagner en productivité, PolymerExpert a développé des tiges à mémoire de forme. Ainsi les boulons sont enfilés facilement sur la tige de faible diamètre. Soumise au chauffage, le diamètre de la tige augmente et vient bloquer les boulons.
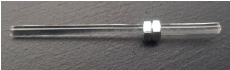
C. Dans le secteur aérospatiale: des bras déployables
Dans une problématique de gain de masse, des dispositifs de déploiement (pour panneaux solaires par exemple) ont été remplacés par des composites à mémoire de forme. Ces matériaux conducteurs thermiquement et électriquement ont la propriété de se déployer simplement grâce à courant électrique apporté par une batterie ou une résistance. L’avantage de cette technologie est d’éviter d’embarquer sur un nano satellite un moteur avec une masse importante, couplé à des bras articulés en métaux.
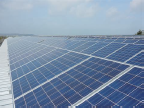